Affordable CO2 Foam Extrusion Board Line Prices
By:Admin
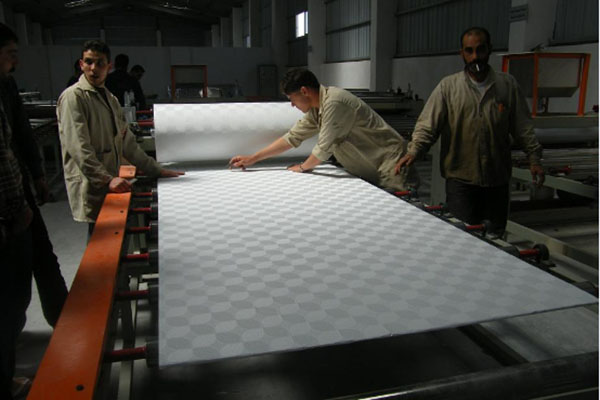
Introduction:
In an era where sustainability and environmental concerns have become paramount, companies across various industries are actively seeking alternatives to reduce their carbon footprint. As a response to these global challenges, a leading manufacturing company has developed an innovative Co2 Foam XPS Extrusion Board Line, poised to revolutionize the construction industry. By offering a highly efficient and eco-friendly solution, this state-of-the-art technology aims to address the growing demand for sustainable building materials.
Body:
1. Introduction to the Co2 Foam XPS Extrusion Board Line:
The Co2 Foam XPS Extrusion Board Line is a cutting-edge manufacturing system that produces extruded polystyrene (XPS) foam boards utilizing carbon dioxide (Co2) as the foaming agent. This groundbreaking technology eliminates the use of commonly employed materials, such as hydrofluorocarbons (HFCs), which are known to have a high global warming potential.
2. Advantages and Features:
a. Reduced Environmental Impact: By leveraging Co2 as the foaming agent, this new-line manufacturing process significantly reduces greenhouse gas emissions. The elimination of HFCs translates into a substantially lower carbon footprint, contributing to a cleaner and more sustainable future for the construction industry.
b. Energy Efficiency: The Co2 Foam XPS Extrusion Board Line boasts enhanced energy efficiency. The system employs advanced temperature and pressure control mechanisms, optimizing the manufacturing process. This results in reduced energy consumption compared to conventional XPS production methods.
c. Superior Thermal Insulation: The foam boards produced by this innovative line possess excellent thermal insulation properties. Their closed-cell structure provides high-density insulation with a low thermal conductivity coefficient, effectively reducing energy consumption in buildings and enhancing overall energy efficiency.
d. Durability and Versatility: The Co2 Foam XPS boards exhibit exceptional durability, making them suitable for various applications. These boards are resistant to moisture, decomposition, and mold growth, ensuring longevity and reliability, even in challenging environmental conditions.
3. Application in the Construction Industry:
a. Building Insulation: The Co2 Foam XPS Extrusion Board Line paves the way for energy-efficient buildings by offering superior insulation capabilities. By minimizing heat transfer through walls, floors, and roofs, these foam boards help reduce heating and cooling demands, resulting in significant energy savings for property owners.
b. Soundproofing: The acoustic properties of the Co2 Foam XPS boards make them valuable in soundproofing applications. They efficiently absorb and dampen sound waves, contributing to a quieter and more comfortable indoor environment.
c. Foundation Protection: The high compressive strength of these foam boards renders them ideal for applications involving foundation protection. Their ability to distribute and bear loads effectively safeguards structures against soil movements and natural disasters.
4. Company Introduction:
[Company Name] is a pioneering manufacturer and industry leader in sustainable building materials. With a commitment to pushing the boundaries of innovation, the company has invested significantly in research and development to create eco-friendly products that meet the needs of a rapidly changing world. By introducing the Co2 Foam XPS Extrusion Board Line, [Company Name] further solidifies its position as a frontrunner in the construction industry's quest for sustainable solutions.
Conclusion:
The introduction of the Co2 Foam XPS Extrusion Board Line represents a significant breakthrough in the construction industry, offering an eco-friendly alternative to traditional insulation materials. By utilizing Co2 as the foaming agent, this advanced manufacturing technology not only reduces greenhouse gas emissions but also provides enhanced energy efficiency and outstanding thermal insulation properties. With its durability, versatility, and application in various construction projects, these Co2 foam boards are poised to revolutionize the way buildings are constructed, paving the way for a greener and more sustainable future.
Company News & Blog
Using Waterproof Calcium Silicate Fiber Cement Board in Construction: A Solution by Jiaheng Board Industry
Title: Fiber Calcium Silicate Board and Fiber Cement Board - The Ideal Waterproof Building MaterialsIntroduction:Jiaheng Board Industry, a renowned manufacturer of fiber calcium silicate board and fiber cement board, has adopted cutting-edge board-making technology to produce high-quality, waterproof, and durable building materials. These innovative construction solutions not only contribute to environmental sustainability but also provide healthier and energy-efficient alternatives for the construction industry. This article will explore the numerous advantages of using fiber calcium silicate board and fiber cement board, their installation process, and the industry-leading manufacturing techniques employed by Jiaheng Board Industry.Advantages of Fiber Calcium Silicate Board and Fiber Cement Board:1. Waterproof: A significant advantage of both fiber calcium silicate board and fiber cement board is their excellent waterproof properties. Whether used in areas prone to moisture, such as bathrooms, kitchens, or exteriors, these building materials provide long-lasting protection against water damage, thereby increasing the lifespan of the structure.2. Fire Resistant: Fiber calcium silicate board and fiber cement board are inherently fire-resistant, making them ideal for applications where fire safety is a concern. These boards effectively resist high temperatures and do not release toxic fumes, providing a safer environment for occupants.3. Durability: Both fiber calcium silicate board and fiber cement board boast exceptional durability, allowing them to withstand impact, extreme weather conditions, and general wear and tear. Their robustness ensures that the building remains intact and aesthetically appealing for an extended period, reducing maintenance costs.4. Versatility: These boards are suitable for a wide range of applications and can be used for both interior and exterior construction projects. They can be easily cut, drilled, and shaped, facilitating creative and versatile architectural designs.Installation Process of Fiber Calcium Silicate Board and Fiber Cement Board:1. Surface Preparation: The installation process begins with ensuring a clean and level surface. Any loose debris or previous coatings should be removed, and the surface should be inspected for potential issues.2. Measuring and Cutting: The boards are measured and marked using appropriate tools. They can be cut using standard woodworking tools or special cutters designed for fiber cement boards.3. Securing the Boards: The boards are then secured to the structure using various methods such as screws, nails, or adhesives. It is essential to follow the manufacturer's guidelines and specifications for proper installation.4. Finishing: Once the boards are securely installed, they can be finished with paint, texture, or other desired finishes to suit the aesthetic requirements of the project.Industry-Leading Manufacturing Techniques by Jiaheng Board Industry:Jiaheng Board Industry, equipped with state-of-the-art board-making technology, places great emphasis on producing high-quality fiber calcium silicate board and fiber cement board. This includes their mineral fiber board making machine, which ensures precise manufacturing and consistent product quality.The company's commitment to environmental sustainability is evident in their extensive use of eco-friendly materials during the board-making process. This ensures that the final product not only meets stringent industry standards but also supports the overall vision of sustainable development.Conclusion:Fiber calcium silicate board and fiber cement board, produced using advanced manufacturing techniques by Jiaheng Board Industry, offer numerous advantages in the construction industry. These waterproof and durable building materials enhance the longevity and safety of structures while promoting environmental sustainability. The ease of installation and versatility of these boards make them a preferred choice for architects, contractors, and homeowners alike. By choosing Jiaheng Board Industry's fiber calcium silicate board and fiber cement board, customers can have confidence in the quality and performance of their construction projects.
Gypsum Ceiling Board Lamination Equipment Offers High-Quality Finishes
article.Oem Gypsum Ceiling Board Lamination Machine Boosts Production Efficiency for Building Material FirmsIn the building material industry, efficiency is vital to meet ever-increasing demand. However, innovative solutions like the Oem Gypsum Ceiling Board Lamination Machine are making resource management smoother and more efficient. The device is gaining popularity among building material companies across the globe due to its ability to enhance board quality and improve production speed.The Oem Gypsum Ceiling Board Lamination Machine serves as an essential tool in the manufacture of gypsum ceiling board. It is an advanced and user-friendly machine that efficiently combines various materials to form a highly durable board. The final product is of high quality with an appealing finish suitable for both commercial and residential buildings.A primary feature of the machine is its computerized control system, which integrates components like the pre-heating chamber, film unwinding system, spray glue machine, film cutting system, and a hydraulic press system. The integration of these components streamlines the manufacturing process, reducing manual labor and increasing the production capacity of the machine.Additionally, the machine boasts an excellent material applicability for various types of ceilings - perforated, non-perforated, suspended, and sound-absorbing acoustic ceiling designs. These features make it a versatile tool that finds application in a broad range of operations.One company leading the development and sales of the Oem Gypsum Ceiling Board Lamination Machine is {}. Based in China, the company has been at the forefront of technological advancement in the gypsum ceiling board industry. It supplies high-quality machines to numerous countries worldwide, serving as a reliable partner to its clients.{}, the Chief Executive Officer of {}, says the company is proud to deliver a revolutionizing product that enhances the production process and saves on costs. "Our Oem Gypsum Ceiling Board Lamination Machine is a game-changer in the building material sector. It is a reliable device that increases efficiency and streamlines the manufacturing process," he states.With the Oem Gypsum Ceiling Board Lamination Machine, building material companies can enjoy numerous benefits. One key advantage is the ability to produce high-quality boards efficiently, reducing lead times and increasing productivity. The automatic control system and integration of the various components facilitate quick and easy operations, leaving room for more production cycles.Moreover, the machine saves on resources like energy costs and lowers the possibility of wastage. Its advanced technology allows for seamless use throughout the lamination process, eliminating the possibility of material damage or inconsistencies.In conclusion, building material companies seeking to boost efficiency and productivity can rely on the Oem Gypsum Ceiling Board Lamination Machine. With its reliable performance, high production capacity, and easy-to-use interface, it is an excellent investment in resource management.The availability of the machine in many countries worldwide, including South Africa, Turkey, Thailand, and many others, guarantees access to the latest technological innovations in the gypsum board industry. The Oem Gypsum Ceiling Board Lamination Machine presents an excellent opportunity for companies to optimize their production processes and increase their competitiveness in the market.%
China Magnesium Oxide Board Manufacturing Machine: A Complete Guide
China Magnesium Oxide Board Machine (hereafter referred to as CMOBM) has recently launched a state-of-the-art production line for the manufacturing of magnesium oxide board. The company's latest offering is set to provide its customers with unmatched quality and durability in modern building materials.CMOBM's new production line is equipped with advanced technology that allows for faster and more efficient production of magnesium oxide boards. This latest technology guarantees the consistent quality of the boards produced, ensuring they meet the highest standards. The production process is also eco-friendly and energy-saving.Magnesium oxide board is a non-toxic, fire-resistant, and soundproof material that is ideal for building construction. It is a versatile material, with a range of uses, from interior and exterior wall cladding, partition walls, flooring, and furniture. Magnesium oxide boards are gaining in popularity among builders, architects, and design professionals for their ease of installation, durability, and stability."CMOBM is committed to providing its customers with the best quality products and services. Our investment in this new production line is a testament to this commitment," said the company spokesperson. "We believe the new technology will help us meet the growing demand for magnesium oxide board in the construction industry."With the increased demand for eco-friendly and sustainable building materials, magnesium oxide boards are emerging as a popular choice in the construction industry. Not only are they durable and long-lasting, but they are also moisture-resistant and do not promote the growth of mold and fungi, making them ideal in high humidity areas.CMOBM's new production line is also set to boost the country's economy by creating jobs and generating revenue. The company has invested heavily in training its staff to ensure they are equipped with the skills needed to operate the new technology efficiently. This investment in human capital will not only benefit the company but also the country's economy as a whole.This latest addition to CMOBM's product portfolio further strengthens the company's standing as an industry leader in the production of magnesium oxide board machines. The company has earned a reputation for its technical expertise, quality products, and excellent customer service.In conclusion, CMOBM's new production line for the manufacturing of magnesium oxide boards is a significant development for the construction industry in China. With increased demand for eco-friendly and sustainable building materials, CMOBM's investment in advanced technology is set to propel the industry forward. The consistently high-quality products that the company produces will lead to more job creation, revenue generation, and a boost to the country's economy. The construction industry can expect to benefit greatly from CMOBM's commitment to providing top-of-the-line products and services.
Top Automatic Factories Producing the Best Gypsum Cornice Designs
Gypsum cornices have been used as a decorative element for centuries. They add elegance and character to any interior space. However, manually producing these ornate designs is a time-consuming and difficult process. To overcome this challenge, several automatic equipment factories have been established. Among these, one of the best gypsum cornice design automatic equipment factories is located in China.This factory, which shall remain unnamed for confidentiality reasons, specializes in the manufacture of gypsum cornice molding machines. With its highly advanced technology, this factory has gained popularity among its customers for its efficiency and quality. The automatic equipment produced by this factory is used in the production of gypsum cornices, which are widely used in interior decoration.The gypsum cornice molding machine produced by this factory is fully automatic and operates with high precision. This equipment eliminates the manual labor and production errors that often occur in traditional methods. In addition, the machine has a high production capacity which means that it can produce a large number of gypsum cornices in a shorter time without sacrificing quality.The factory uses high-quality raw materials to manufacture its machinery. The machines are made of sturdy materials that ensure the long life span of the production equipment. The factory also has strict quality control measures in place during the production process. This quality control ensures that the machinery produced is of the highest standard.The gypsum cornice molding machine produced by this factory can produce various designs and sizes of gypsum cornices. The machine can produce classic, contemporary, and customized designs. This production flexibility makes it an ideal solution for contractors and designers seeking a customizable finishing touch to their projects.The factory also provides training and after-sales services to its clients. This support ensures that clients can use the equipment properly and efficiently. It also provides assistance if there are any issues with the equipment.The gypsum cornices produced using the automatic equipment from this factory are in high demand across the world. The cornices produced are of superior quality and are used in various settings, including commercial, residential, and public spaces. The gypsum cornice design automatic equipment factory is known for its commitment to excellence and innovation. The use of technology to produce gypsum cornices has revolutionized the industry, and this factory is leading the way in this expansion of the industry.The factory's commitment to quality and innovation has made it a leader in the industry. The use of automatic equipment has made the production process efficient and cost-effective. The factory has been able to provide quality products to the market at competitive prices. This commitment to quality has earned the factory a strong reputation and a loyal customer base.The use of gypsum cornices in interior design is growing, and this factory is poised to take advantage of this upward trend. With its state-of-the-art technology and commitment to quality, this factory is positioned to remain as a leader in the industry for many years to come.In conclusion, the best gypsum cornice design automatic equipment factory, located in China, is using advanced technology to produce high-quality gypsum cornices. Their commitment to excellence and innovation has made them a leader in the industry. Their machines are efficient, cost-effective, and produce superior quality gypsum cornices. Their dedication to quality and service has earned them a loyal customer base. They have positioned themselves to remain at the forefront of the industry, contributing to the growth of the gypsum cornice industry.
Foam Board Making Machines: An Introduction to Manufacturing Xps Boards
XPS Foam Board Making Machine Factories Revolutionizing the Insulation IndustryIn today's eco-conscious world, energy efficiency and conservation have become increasingly important. As a result, the demand for innovative and high-quality insulation materials has skyrocketed. One such material that has gained significant popularity is XPS foam board. And to meet the growing demand, XPS Foam Board Making Machine factories (name removed) have emerged as industry leaders.XPS foam board, short for Extruded Polystyrene Foam Board, is a type of insulation material renowned for its superior thermal performance and moisture resistance. It is commonly used in various applications such as underfloor heating, wall insulation, and roof insulation. The process of manufacturing XPS foam boards requires advanced machinery, precision, and expertise, which are now readily available at factories equipped with XPS Foam Board Making Machines.With years of experience and a deep understanding of the insulation industry, these XPS Foam Board Making Machine factories have become pioneers in producing high-quality insulation materials. Their state-of-the-art machinery and technology ensure that the end products meet the strictest industry standards and regulations. Moreover, they have successfully developed innovative manufacturing techniques that help reduce energy consumption, minimize waste, and improve overall efficiency.One crucial aspect that sets these XPS Foam Board Making Machine factories apart is their commitment to environmental sustainability. Their goal is not only to provide top-notch insulation materials but also to reduce the carbon footprint associated with their production. These factories adhere to the highest environmental standards and employ eco-friendly manufacturing processes, including recycling and reusing waste generated during the production of XPS foam boards.Furthermore, these factories prioritize research and development to continuously enhance the performance and quality of their XPS foam boards. They work closely with engineers, scientists, and industry experts to stay at the forefront of insulation technology. This collaborative approach allows them to introduce new features and improvements in their products regularly, ensuring that they remain competitive in the market.In addition to their commitment to innovation, these XPS Foam Board Making Machine factories also prioritize customer satisfaction. They understand the diverse needs of their clients and strive to provide customized solutions tailored to specific requirements. Whether it is for residential, commercial, or industrial applications, these factories can manufacture XPS foam boards of different sizes, thicknesses, and densities to meet the unique insulation needs of their customers.To further solidify their reputation, these XPS Foam Board Making Machine factories provide comprehensive customer support and after-sales services. They have a dedicated team of professionals who are readily available to address any queries, provide technical assistance, and ensure a smooth and hassle-free experience for their clients. This commitment to customer service has earned them a loyal customer base that continues to grow with each passing year.The success of these XPS Foam Board Making Machine factories can be attributed not only to their advanced machinery and cutting-edge technology but also to their skilled workforce. These factories employ highly trained technicians, engineers, and production personnel who possess in-depth knowledge of the insulation industry. Their expertise combined with continuous training helps maintain the highest standards throughout the manufacturing process, resulting in superior quality XPS foam boards.In conclusion, the rise of XPS Foam Board Making Machine factories has revolutionized the insulation industry. By harnessing advanced technology, ensuring environmental sustainability, and prioritizing customer satisfaction, these factories have become leaders in manufacturing high-quality XPS foam boards. As the demand for energy-efficient insulation continues to increase, these factories are well-equipped to meet the needs of a rapidly evolving market.
Lightweight Wall Panel Production Line for Mgo Board - Benefits and Cost Analysis
Jinan Zhongke Building Material Machinery Co., Ltd., a leading building material machinery manufacturer in China, has recently launched its latest Mgo Board Light Weight Wall Panel Production Line. The product line is designed to produce high-quality wall panels that are lightweight, fire-resistant, waterproof, and energy-efficient.The company has invested heavily in research and development to create a leading-edge Mgo Board Light Weight Wall Panel Production Line that is capable of producing wall panels of up to 3660mm*1220mm*3mm size at a rate of 1-30m/min. The production line is energy-efficient, cost-effective, and requires minimal labor for operation.According to the benefit analysis conducted by Jinan Zhongke Building Material Machinery Co., Ltd., the cost accounting for producing one wall panel includes raw material cost, water-electricity fee, and labor cost. The raw material cost for one panel is 15 yuan/piece, which is significantly lower than the price of traditional wall panels. The water-electricity fee is 0.2 yuan/piece, and the labor cost is 1.5 yuan/piece. Therefore, the total cost for one panel is 16.7 yuan/piece, which is much lower than the cost of traditional wall panels.Moreover, the Mgo Board Light Weight Wall Panel Production Line is fully automated, requiring only two workers for its operation. Thus, the labor cost is reduced, leading to higher profits for the manufacturers. The production line also has a low energy consumption rate, which reduces the overall manufacturing costs and is environmentally friendly.Jinan Zhongke Building Material Machinery Co., Ltd. is a reputable manufacturer that prioritizes customer satisfaction. The company has a team of experienced and professional engineers who provide customization services to meet the specific requirements of its clients.The Mgo Board Light Weight Wall Panel Production Line is suitable for manufacturing various types of lightweight wall panels, including partition walls, external walls, internal walls, and fire-resistant walls. The wall panels can be used in various residential and commercial buildings, such as hotels, schools, hospitals, and office complexes.In conclusion, Jinan Zhongke Building Material Machinery Co., Ltd.'s latest Mgo Board Light Weight Wall Panel Production Line is a revolutionary product that will transform the construction industry. It is cost-effective, energy-efficient, and produces high-quality wall panels that have numerous benefits over traditional wall panels. The product line's superior quality design, advanced technology, and customization services set it apart from its competitors, making it the go-to product for all lightweight wall panel needs.
Efficient Production Line for Mineral Fiber Ceiling Tiles Boosts Manufacturing Process
[Company Name], a leading manufacturer in the construction industry, has recently launched their state-of-the-art Mineral Fiber Ceiling Tiles Production Line. This advanced production line is set to revolutionize the production process of mineral fiber ceiling tiles, providing customers with high-quality and cost-effective solutions for their construction and interior design needs.With years of experience in the industry, [Company Name] has become renowned for their commitment to innovation and excellence. The introduction of their new Mineral Fiber Ceiling Tiles Production Line is a testament to their dedication to providing cutting-edge solutions to their customers.The production line boasts the latest technology and machinery, allowing for efficient and streamlined manufacturing processes. This ensures that each mineral fiber ceiling tile produced is of the highest quality, meeting industry standards and regulations. By incorporating advanced automation systems, the production line also improves productivity and reduces human error, resulting in increased efficiency and reliability.Mineral fiber ceiling tiles are highly sought-after in the construction and interior design sectors due to their numerous benefits. These ceiling tiles are known for their excellent acoustic properties, providing sound insulation and improving the overall acoustics of a space. Additionally, mineral fiber ceiling tiles offer superior fire resistance, making them a safe choice for various commercial and residential applications.[Company Name]'s Mineral Fiber Ceiling Tiles Production Line is capable of producing a wide range of ceiling tiles in different sizes, designs, and finishes. This versatility allows customers to choose the perfect ceiling tiles that complement their interior aesthetics while fulfilling their functional requirements.The implementation of this advanced production line also underscores [Company Name]'s commitment to sustainability. The manufacturing process of mineral fiber ceiling tiles incorporates eco-friendly practices, minimizing waste and reducing the carbon footprint. By investing in this production line, [Company Name] further solidifies their position as an environmentally responsible industry leader.Commenting on the launch, [Spokesperson Name], the CEO of [Company Name], expressed their excitement about the new production line, stating, "We are thrilled to introduce our Mineral Fiber Ceiling Tiles Production Line to the market. This state-of-the-art facility will allow us to meet the growing demand for high-quality, sustainable ceiling tiles while maintaining our commitment to innovation and customer satisfaction."As the construction industry continues to evolve, [Company Name] remains at the forefront of advancements, continuously striving to provide innovative solutions to their customers. With the launch of their Mineral Fiber Ceiling Tiles Production Line, they are expected to further strengthen their position as a market leader in the production of high-quality construction materials.Customers can now rely on [Company Name] for premium mineral fiber ceiling tiles that offer a perfect blend of functionality, aesthetics, and sustainability. Whether it's for commercial spaces, educational institutions, healthcare facilities, or residential projects, their extensive range of ceiling tiles will meet the diverse needs of different sectors.In conclusion, [Company Name]'s introduction of the Mineral Fiber Ceiling Tiles Production Line is set to redefine the production process and quality standards of mineral fiber ceiling tiles. With their commitment to innovation, sustainability, and customer satisfaction, [Company Name] continues to play a pivotal role in shaping the future of the construction industry.
Revolutionizing Mgo Board Production: China's Advanced Automatic Production Line
Title: Advanced Automatic MGO Board Production Line Revolutionizes Manufacturing Industry in ChinaIntroduction:China's manufacturing industry has received a major boost with the introduction of an advanced automatic MGO (Magnesium Oxide) Board Production Line. This ground-breaking technology has already taken the country by storm, streamlining operations and revolutionizing the production of MGO boards. The automated production line is a significant development, reflecting China's commitment to innovation and sustainable manufacturing practices.The company, which specializes in the design and manufacture of cutting-edge machinery, has invested considerable resources into research and development to create this state-of-the-art production line. By adopting the latest technological advancements and adhering to stringent quality control standards, they have successfully developed an automated system that improves efficiency, reduces labor costs, and enhances the overall production process.Streamlined Production Process:The advanced automatic MGO Board Production Line incorporates a range of innovative features, significantly increasing the efficiency of the production process. Robotics and AI technology have been implemented to automate various stages of manufacturing, starting from raw material inspection, mixing, and board formation, all the way to final quality control checks. This fully automated system reduces the need for manual intervention, minimizing errors and inconsistencies, and ensuring uniformity in each board produced.The implementation of robotics and AI technology also contributes to a reduction in labor costs and significantly increases productivity. With the automated production line in place, more boards can be manufactured within a shorter timeframe, meeting the ever-increasing demand for MGO boards in China's construction and interior design industries.Quality Control and Product Consistency:Apart from enhancing production efficiency, the automated MGO Board Production Line also focuses on maintaining the highest quality standards. The integration of AI-powered quality control systems ensures that every board produced meets the required specifications. Real-time monitoring and inspection throughout the production process guarantee that only superior quality boards reach the market, building trust and satisfaction among consumers.Sustainable Manufacturing:In line with China's commitment to sustainable development, the advanced automatic MGO Board Production Line incorporates eco-friendly practices. The system optimizes the usage of raw materials, minimizing waste and promoting resource efficiency. Moreover, the production line is designed to reduce energy consumption and minimize environmental impact, aligning with China's green goals and global sustainability initiatives.Market Impact:The introduction of this advanced technology is expected to have a profound impact on the MGO board manufacturing industry in China. With increased production capacity, enhanced automation, and improved product consistency, manufacturers using this production line will be able to meet growing market demands effectively. The automated production process will also enable manufacturers to deliver their products in a more timely manner, further strengthening their market position and competitiveness.Looking to the Future:The successful development and adoption of the advanced automatic MGO Board Production Line mark a significant milestone for the company and the manufacturing industry in China as a whole. With continuous improvements and technological advancements, this production line will likely become a benchmark for the industry, driving further growth and innovation.Conclusion:The introduction of an advanced automatic MGO Board Production Line signifies China's commitment to technological innovation and sustainable manufacturing practices. The automated system ensures streamlined production, superior product consistency, and reduced environmental impact. By revolutionizing the manufacturing process, this groundbreaking technology paves the way for a more efficient and sustainable future for MGO board production in China.
Customized Abs Board Extrusion Line for XPS Heat Insulation Foamed Plate Production
Qingdao JBD Machinery is a leading manufacturer and supplier of extrusion lines that are used to produce various types of foam boards. With the advanced technology and cutting-edge machinery, the company provides a diverse range of innovative and high-performance extrusion lines to meet the growing demands of the market. The Factory Customized Abs Board Extrusion Line and XPS Heat Insulation Foamed Plate Production Line are some of its popular products with excellent performance and high reliability.The Factory Customized Abs Board Extrusion Line is designed to produce high-quality ABS foam boards, which can be used in a variety of applications such as automotive dashboards, instrument panels, and interior parts. The machine is equipped with a high-quality screw and barrel that ensures the homogeneity and consistency of the mixing process. The production line is also equipped with a precision cut-off system that produces a precise cut and ensures the uniformity of the board thickness.The XPS Heat Insulation Foamed Plate Production Line is one of the best products offered by Qingdao JBD Machinery. The extrusion line is designed to produce lightweight and strong XPS foamed boards, which are widely used as heat insulation and soundproofing materials in construction, refrigeration, and packaging industries. The board offers incomparable heat insulation traits, non-water absorption, high compressive strength, excellent heat preservation performance, and low cost. The foamed plate production line is easy and quick to execute, making it an ideal solution for various industrial applications.The XPS Heat Insulation Foamed Plate Production Line is a fully automatic extrusion line with high productivity and efficiency. The machine is equipped with a high-quality screw and barrel that ensures the uniformity of the foaming process and the homogeneity of the foam structure. The production line also features a precise cutting system that produces high-quality foam boards with uniform thickness and size. The machine can be customized according to customer requirements and can produce boards of different sizes and shapes.Qingdao JBD Machinery is committed to providing customers with high-quality products and services. The company has a team of highly qualified professionals who have extensive experience in manufacturing and designing extrusion lines. The company also provides excellent after-sales service to ensure customer satisfaction. As a leading manufacturer in China, the company has been exporting its products to different parts of the world, including North America, South America, Europe, Asia, Africa, and Oceania. The company has established long-term relationships with its customers by providing them with high-quality products, prompt delivery, and excellent service. In conclusion, Qingdao JBD Machinery is a reputable and reliable manufacturer of extrusion lines that produces high-quality products such as Factory Customized Abs Board Extrusion Line and XPS Heat Insulation Foamed Plate Production Line. The company is committed to providing innovative and cost-effective solutions to its customers, and its products are widely used in various industrial applications. With its cutting-edge technology and excellent service, Qingdao JBD Machinery is poised to become a leading player in the extrusion line manufacturing industry.
Updated Report on PVC Gypsum Ceiling Board Market Status and Future Outlook
The construction industry has become one of the fastest-growing industries in the world, and it is expected to continue to rise in the coming years. With the increasing demand for sustainable and efficient building materials, the use of gypsum ceiling board has been gaining widespread attention. One of the most popular types of gypsum ceiling board is the PVC gypsum ceiling board, which is commonly used in commercial spaces, offices, and residential homes. The PVC gypsum ceiling board is a type of false ceiling made from gypsum plaster and a paper or fiberglass mat. The plaster is sandwiched between two layers of paper or fiberglass, with the top layer being a PVC film. This PVC film not only enhances the aesthetic appeal of the ceiling board but also provides protection against water and moisture damage. The PVC gypsum ceiling board also has many advantages over other types of ceiling boards. It is lightweight, easy to install, and does not require a lot of maintenance. It is also fire-resistant, making it a safe option for buildings that need additional protection against fire. Additionally, PVC gypsum ceiling boards have acoustic properties that help to reduce noise levels within a room. To produce the PVC gypsum ceiling board, a gypsum ceiling pressing machine is used in factories. This machine is a critical component of the manufacturing process, and it ensures that the ceiling board is produced according to the required specifications. The machine applies pressure to the gypsum plaster and the paper or fiberglass mat, forming the desired shape and thickness of the ceiling board. The PVC gypsum ceiling board market is expected to experience significant growth in the coming years due to the ongoing construction activities in different parts of the world. As more buildings are constructed, the demand for ceiling boards is also expected to increase. Additionally, the need for energy-efficient and sustainable building materials is also expected to boost the demand for PVC gypsum ceiling boards. In conclusion, PVC gypsum ceiling board is a popular type of false ceiling, and it is expected to become even more popular in the coming years. With its many advantages, including fire resistance and acoustic properties, it is an excellent option for commercial and residential buildings. To produce these ceiling boards, gypsum ceiling pressing machine factories play a crucial role in ensuring that the products meet the required specifications. As the demand for PVC gypsum ceiling boards continues to rise, it is vital for factories to continue to produce high-quality products.