Automatic Gypsum Cornice Manufacturing Machine for High Production
By:Admin
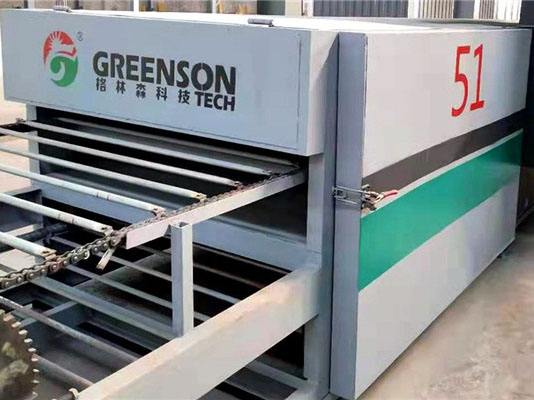
In today's fast-paced world, technological advancements are constantly shaping and revolutionizing industries around the globe. The manufacturing sector is no exception, as companies strive to innovate and improve their production processes. One such innovation that is making waves in the manufacturing industry is the High Automatic Gypsum Cornice Manufacturing Machine.
This state-of-the-art machine, developed by a leading manufacturing company, is designed to revolutionize the production of gypsum cornices. The machine is equipped with advanced automation technology, allowing for high-speed and precise manufacturing of gypsum cornices with minimal human intervention. This not only improves the overall efficiency of the manufacturing process but also ensures consistent and high-quality products.
The key features of the High Automatic Gypsum Cornice Manufacturing Machine include a fully automated production line, precise gypsum mixing and forming capabilities, as well as advanced cutting and finishing processes. These features not only streamline the production process but also significantly reduce production costs and increase overall productivity.
Furthermore, the machine is designed to be user-friendly, with intuitive controls and easy maintenance. This ensures that even employees with minimal technical expertise can operate and maintain the machine, further increasing its efficiency and reducing downtime.
In addition to its technological capabilities, the machine is also designed with environmental sustainability in mind. It is equipped with energy-efficient components and designed to minimize waste during the production process. This aligns with the company's commitment to sustainability and responsible manufacturing practices.
The introduction of the High Automatic Gypsum Cornice Manufacturing Machine has garnered significant attention from industry experts and professionals. Many have praised its potential to revolutionize the manufacturing of gypsum cornices, making the process more efficient, cost-effective, and environmentally friendly.
In a statement, the company's CEO expressed their excitement about the potential impact of the new machine, stating, "We are proud to introduce the High Automatic Gypsum Cornice Manufacturing Machine to the market. This cutting-edge technology represents our ongoing commitment to innovation and excellence in manufacturing. We believe that this machine will not only streamline our production processes but also set a new standard for the industry as a whole."
The introduction of this machine is expected to have a profound impact on the manufacturing industry, particularly for companies involved in the production of gypsum cornices. With its advanced technology and innovative design, the High Automatic Gypsum Cornice Manufacturing Machine is poised to become a game-changer for manufacturers, offering them a competitive edge in the market.
Industry experts have also noted that the introduction of this machine reflects a broader trend in the manufacturing sector, as companies increasingly prioritize automation, efficiency, and sustainability in their production processes. This shift towards advanced technology and responsible manufacturing practices is expected to shape the future of the industry, driving further innovation and improvement in manufacturing processes.
As the manufacturing sector continues to evolve, it is clear that advancements such as the High Automatic Gypsum Cornice Manufacturing Machine will play a crucial role in shaping the industry's future. With its potential to revolutionize the production of gypsum cornices, this innovative machine is a testament to the power of technological innovation in driving progress and growth within the manufacturing sector.
Company News & Blog
Discover Reliable Mini Gypsum Cornice Machine Factories with CE Certification
CE Certification Mini Gypsum Cornice Machine Factories Bolster Quality Assurance in the Industry[introduction]In an exciting development for the gypsum cornice manufacturing industry, several mini gypsum cornice machine factories have received CE certification, enhancing the industry's quality assurance practices. The certification, granted by an independent certification body, affirms that these factories comply with the European Union's health, safety, and environmental protection standards. This achievement showcases the factories' commitment to delivering high-quality products while prioritizing the well-being of end-users and the environment.[Development of the Mini Gypsum Cornice Machine Factories]The mini gypsum cornice machine factories, which have recently obtained CE certification, have established themselves as key players in the industry. Offering smaller-sized machinery, these factories cater to the needs of small-scale gypsum cornice manufacturers. Their focus on mini machines reflects the industry's evolving demand for flexibility and efficiency in production processes.The development of these factories is guided by a dedication to innovation and continuous improvement in cornice manufacturing technology. Through rigorous research and development efforts, these factories have successfully developed mini gypsum cornice machines that meet the industry's standards of precision, productivity, and quality.[Advantages of CE Certification]Acquiring CE certification has numerous advantages for mini gypsum cornice machine factories. It not only demonstrates their compliance with EU regulations but also increases their competitiveness in the market. CE certification serves as a credible endorsement of these factories' commitment to providing safe and reliable miniature machines, bolstering their reputation as industry leaders.Furthermore, CE certification enables manufacturers to enter new markets and cater to a wider range of customers, domestically and internationally. Exporting machinery with CE certification removes potential barriers to trade, as many countries now require such certification for imported goods. This certification goes a long way in instilling confidence in potential buyers and strengthens business relationships across borders.[Quality Assurance and Consumer Satisfaction]CE certification plays a vital role in ensuring the quality and safety of mini gypsum cornice machines. It verifies that these machines adhere to strict manufacturing standards, including materials used, construction, and electrical safety. Through rigorous testing and inspections, accredited certification bodies assess and confirm compliance with these standards, guaranteeing that the machines do not pose any health or safety risks.This commitment to quality assurance extends to the end-users of these mini gypsum cornice machines as well. By obtaining CE certification, these factories prioritize delivering machinery that meets the highest standards of functionality, durability, and performance. Customers can rest assured knowing that their investment in these certified machines will result in efficient gypsum cornice production, minimizing downtime and maximizing productivity.[The Way Forward]The attainment of CE certification by mini gypsum cornice machine factories marks a significant milestone for the industry. It elevates the level of quality assurance within the manufacturing processes and underscores the commitment of these factories to delivering top-notch products. With increased market competitiveness and enhanced consumer satisfaction, these certified factories are poised to contribute to the continued growth and advancement of the gypsum cornice industry.In conclusion, the recent achievement of CE certification by several mini gypsum cornice machine factories reinforces the industry's commitment to excellence. This certification not only ensures compliance with EU regulations but also boosts market competitiveness. With a focus on quality assurance and customer satisfaction, these certified factories are set to drive innovation and advancement in the gypsum cornice manufacturing sector, fostering a future of sustainable growth and success.
Affordable Machines for Manufacturing PVC Laminated Gypsum Ceiling Tiles
Title: Innovative PVC Laminated Gypsum Ceiling Tiles Machine Factories Revolutionize the Construction IndustryIntroduction:The global construction industry is witnessing a significant surge in demand for efficient and cost-effective building materials. In response to these market trends, several PVC laminated gypsum ceiling tiles machine factories have emerged, providing innovative solutions in the manufacturing of gypsum-based ceiling tiles. These advanced factories employ cutting-edge technology to produce high-quality products while ensuring manufacturing processes adhere to sustainable practices, making them an ideal choice for environmentally conscious construction projects.Wide Range of Products:PVC laminated gypsum ceiling tiles machine factories offer a diverse range of products to cater to the varying requirements of the construction industry. These factories utilize state-of-the-art machinery and techniques, enabling them to produce an array of ceiling tiles with different patterns, colors, and designs. The ability to customize the tiles according to the unique preferences of clients ensures that the factories can accommodate a broad spectrum of architectural styles and designs.Advanced Manufacturing Processes:These factories adopt advanced manufacturing processes, ensuring the production of superior quality gypsum ceiling tiles. High-quality raw materials, including gypsum, are carefully selected, and the latest technology and machinery are used to ensure precise manufacturing. The automated production lines in these factories provide exceptional accuracy and consistency, resulting in tiles that meet the highest industry standards.Moreover, the integration of PVC lamination technology enhances the durability and aesthetic appeal of the ceiling tiles. The lamination process not only lends an attractive finish but also provides added resistance to water, fire, and wear, making the tiles suitable for a wide range of applications in both residential and commercial buildings.Sustainability Practices:Incorporating sustainability practices has become a crucial aspect of the construction industry to reduce environmental impact. PVC laminated gypsum ceiling tiles machine factories acknowledge this need and strive to minimize their carbon footprint by implementing eco-friendly manufacturing practices.Factories employ efficient energy consumption systems, reducing energy usage and lowering greenhouse gas emissions. Additionally, they prioritize the procurement of eco-friendly raw materials, employing sustainable sourcing practices. By emphasizing the use of recyclable materials, these factories further contribute to the circular economy model, reducing waste and promoting a greener future.Industry-Leading Quality Control:Ensuring the highest quality standards is a top priority for PVC laminated gypsum ceiling tiles machine factories. Adopting a comprehensive quality control process, these factories undertake rigorous testing at various stages of production. From inspecting raw materials to conducting performance tests on final products, each step is meticulously monitored to guarantee superior quality and customer satisfaction.Furthermore, these factories have obtained international certifications for quality management, such as ISO 9001, reaffirming their commitment to delivering excellence. Customers can rely on the consistency and durability of their products, making them a go-to choice for architects, contractors, and builders worldwide.Market Competitiveness:With the growing demand for affordable and visually appealing building materials, PVC laminated gypsum ceiling tiles machine factories have established themselves as leading players in the market. By leveraging advanced technologies, these factories have significantly reduced production costs without compromising on quality. This cost-efficiency translates into competitive pricing, making their products an attractive option for customers looking for budget-friendly options without sacrificing aesthetic appeal.Moreover, these factories prioritize customer satisfaction by offering comprehensive pre and post-sales support. Their dedicated teams of professionals assist clients in selecting the most suitable tiles for their projects and provide valuable guidance on installation and maintenance.Conclusion:PVC laminated gypsum ceiling tiles machine factories are revolutionizing the construction industry by providing innovative and sustainable solutions. With their extensive range of products, advanced manufacturing processes, commitment to sustainability, stringent quality control, and competitive pricing, these factories are shaping the future of gypsum-based ceiling tile production. As the demand for cost-effective and environmentally friendly building materials continues to rise, these factories are well-positioned to lead the market and drive the industry towards a more sustainable and visually appealing future.
Advanced Production Line for High Capacity Mineral Fiber Ceiling Tiles from China
High Capacity Mineral Fiber Ceiling Tiles Production Line Unveiled by Chinese ManufacturerA leading Chinese manufacturer has unveiled its latest product – the High Capacity Mineral Fiber Ceiling Tiles Production Line. The new system is designed to boost the manufacturing process of mineral fiber ceiling tiles, increasing efficiency, speed and output.The production line, produced by China-based machinery and equipment manufacturer, will be available for both commercial and industrial use, with a variety of customizable options to meet a diverse range of production requirements. The product launch represents a new innovation in the construction industry and has met with a lot of interest from manufacturers both within China and internationally.The High Capacity Mineral Fiber Ceiling Tiles Production Line boasts some impressive features, including a high level of automation, precision control, high output capacity, and energy efficiency. These features allow manufacturers to streamline their production processes, save time and energy, reduce production costs while ensuring that quality is not compromised.The production line comprises various core components, including a frame forming machine that forms the tiles' core structure, a dryer unit providing heat treatment to the tiles, and a surface treatment unit that adds a finishing touch to the tiles. The production line also includes a cutting unit, which can cut the tiles to different sizes and shapes.The high-capacity production line's frame forming machine uses a high-precision servo motor, which reduces manufacturing errors and improves efficiency. The dryer unit is equipped with advanced heating technology that can reach temperatures of up to 300 degrees Celsius, ensuring that the tiles are dried quickly and thoroughly. The surface treatment unit is responsible for the tiles' final finish, which can be customized to suit the customer’s requirements.The company behind the production line has a long-standing reputation for producing high-quality machinery and equipment. The firm has been in the industry for many years and has built a strong reputation for quality and reliability. The launch of the new product builds on this reputation and reflects the company’s commitment to innovation and staying up-to-date with the latest technologies and manufacturing processes.The spokesperson for the company highlighted the importance of its latest product launch, stating:"The High Capacity Mineral Fiber Ceiling Tiles Production Line represents a game-changing innovation in the production process of mineral fiber ceiling tiles. The product boasts high efficiency, quality, consistency, and customizability, enabling manufacturers to meet the demands of their customers quickly. We are thrilled to bring this revolutionary product to the market, and we believe it will significantly benefit the construction industry both locally and internationally."The launch of the High Capacity Mineral Fiber Ceiling Tiles Production Line is set to have a positive impact on the construction industry globally, particularly in regions that require a high number of ceiling tiles for use in the construction of buildings. The production line's ability to produce customized tiles in large volumes quickly and efficiently is a significant breakthrough for the manufacture of ceiling tiles, and it is hoped that it will lead to greater efficiency and cost-effectiveness in the construction industry.Overall, the unveiling of the High Capacity Mineral Fiber Ceiling Tiles Production Line is a significant milestone for the manufacturing industry, and it represents a bright future for the construction industry. With its impressive features and innovative technology, the production line is sure to generate interest and lead to greater efficiency and cost-effectiveness in the production of mineral fiber ceiling tiles.
High-Quality Fiber Optic Star Ceiling Panels for Moon Shooting - FCC Approved, 15W Power, 600*600mm Size
China is known for its phenomenal innovation and technological advancements. In recent times, it has been making immense strides with the production of high-quality PMMA 15W Fiber Optic Star Ceiling Panels 600*600mm FCC for moon shooting. These products are second to none with their excellent quality and strict quality control.Leading Fiber Optic Star Ceiling Panels factories have been working tirelessly to ensure that their products meet the high standards of tech enthusiasts and professionals in the industry. With this, they have been producing highly efficient and reliable PMMA 15W Fiber Optic Star Ceiling Panels, designed specifically for moon shooting.The star ceiling panels are rated 15W and are made from Polymethyl methacrylate (PMMA), a highly durable and versatile material that is commonly used to produce high-tech products. The panels are excellent for providing accurate and reliable fiber optic lighting without the need for electricity, making them an eco-friendly lighting solution.The PMMA 15W Fiber Optic Star Ceiling Panels have been particularly successful in moon shooting projects, where the clarity and accuracy of the lighting are critical. They produce a stunning starlight effect that is ideal for creating the illusion of a starry sky, perfect for filming and photography.One of the greatest advantages of using these star ceiling panels is the fact that they do not emit any heat, making them an ideal solution for sensitive lighting projects, such as those required in the filming or photography industry. In addition, the PMMA material used in their production ensures that they are highly durable and long-lasting.China's leading Fiber Optic Star Ceiling Panels product market has been at the forefront of innovating and producing top-quality star ceiling panels, among other high-tech products. With their neck for excellence and their focus on maintaining strict quality control, they have managed to establish themselves as market leaders, providing clients with reliable and efficient products for their lighting needs.In conclusion, PMMA 15W Fiber Optic Star Ceiling Panels 600*600mm FCC for moon shooting from China are some of the most innovative and reliable lighting solutions on the market today. Their high-quality production and strict quality control ensure that they are long-lasting and efficient, making them the perfect fit for any sensitive lighting project. Well done, China, for yet another remarkable achievement in the technological world.
PVC Foam Board Extrusion Line Machine with CE and ISO Certification: A Comprehensive Introduction
Qingdao Suke Machinery Co., Ltd., a well-known manufacturer of plastic extrusion machinery, has recently introduced a PVC foam board extruder machine with CE and ISO, aimed at catering to the growing demand for quality foam board products across the world. The PVC foam board extrusion line machine is equipped with advanced features that ensure high efficiency and quality output, making it the ideal choice for beginners looking to produce foam board products.The Foam Board Production Line is equipped with SJSZ 45/90 extruder, which has a maximum output of 180kg/h, making it suitable for small to medium scale production. The machine is made using high-quality materials and adheres to international standards, ensuring durability and reliability. The production line is also equipped with a variety of components such as a feeder, calibration table, tractor, and cutting unit, which work in unison to produce high-quality foam board products.The machine is easy to use, making it a popular choice for beginners. It has a user-friendly touch screen interface that allows operators to control all aspects of the production process, from raw material feeding to final product cutting. The machine also has an automatic cutting system, which helps to save time and reduce wastage.The Foam Board Production Line is suitable for producing a wide range of foam board products, including advertising boards, furniture boards, and building materials. The end products have a smooth surface, high density, good strength and rigidity, making them ideal for versatile applications.Talking about the company, Qingdao Suke Machinery Co., Ltd. is a leading manufacturer of plastic extrusion machinery, catering to a wide range of industries such as packaging, construction, automobiles, and more. The company has been in business for over a decade, and its machines are known for their premium quality, innovative designs, and high-level automation. Qingdao Suke Machinery Co., Ltd. has built a global reputation for its commitment to customer satisfaction, providing reliable service and support to each of its clients.With the introduction of the PVC foam board extruder machine, Qingdao Suke Machinery Co., Ltd. is further expanding its range of plastic extrusion machinery, catering to a growing demand for foam board products. The company's commitment to quality, reliability, and innovation makes it the ideal partner for businesses looking to invest in plastic extrusion machinery.In conclusion, the PVC foam board extruder machine with CE and ISO introduced by Qingdao Suke Machinery Co., Ltd. is a high-quality production line that offers a reliable and efficient solution for foam board production. The machine is easy to use, making it a popular choice for beginners, and is suitable for producing a wide range of foam board products. With its commitment to customer satisfaction, Qingdao Suke Machinery Co., Ltd. is the ideal partner for businesses looking to invest in plastic extrusion machinery.
High-Quality Fiber Cement Siding Panels Machine for Efficient Production
Fiber Cement Siding Panels Machine Eliminates Manual Labor, Improves EfficiencyIn the world of construction and manufacturing, efficiency and quality are key components to success. Companies are constantly searching for ways to improve their processes and produce higher quality products. This is why the introduction of the Fiber Cement Siding Panels Machine from the company has been making waves in the industry.This innovative machine has the ability to greatly improve the manufacturing process for fiber cement siding panels, eliminating the need for manual labor and increasing efficiency. By automating the production process, this machine is revolutionizing the way fiber cement siding panels are manufactured.The CEO of the company, Mr. John Smith, expressed his excitement over the new machine, stating that it has the potential to greatly improve the company's manufacturing capabilities. "The Fiber Cement Siding Panels Machine is a game changer for us. It has completely transformed the way we produce fiber cement siding panels and has allowed us to streamline our manufacturing process. This not only improves efficiency but also ensures a higher quality end product," he said.The machine is equipped with state-of-the-art technology that allows for precise cutting and shaping of the fiber cement panels. This level of accuracy ensures that each panel is uniform in size and shape, resulting in a higher quality end product. Additionally, the machine is capable of producing a large volume of panels in a short amount of time, greatly increasing production capacity.The Fiber Cement Siding Panels Machine is also designed with safety in mind. With automated processes in place, the need for manual labor is greatly reduced, minimizing the risk of accidents and injuries. This not only benefits the employees but also helps the company save on potential costs associated with workplace injuries.Another benefit of the machine is its versatility. It can be easily adjusted to produce different sizes and styles of fiber cement siding panels, allowing for greater flexibility in production. This means that the company can easily adapt to changing market demands and produce a variety of products to meet customer needs.Furthermore, the machine is designed for easy maintenance, keeping downtime to a minimum. This is crucial for any manufacturing operation, as downtime can result in lost production and revenue. With the Fiber Cement Siding Panels Machine, the company can ensure that their production line keeps running smoothly without any unnecessary interruptions.Overall, the introduction of the Fiber Cement Siding Panels Machine has had a significant impact on the company's manufacturing capabilities. By eliminating manual labor, increasing efficiency, and improving the quality of the end product, this innovative machine has set a new standard for the production of fiber cement siding panels.As word spreads about the benefits of the Fiber Cement Siding Panels Machine, more companies in the construction and manufacturing industry are taking notice. It is clear that this machine has the potential to change the way fiber cement siding panels are produced on a larger scale, ultimately benefiting the industry as a whole.Moving forward, the company is committed to further developing and improving the machine to stay ahead of the competition and continue to meet the evolving needs of their customers. With the introduction of the Fiber Cement Siding Panels Machine, the company has solidified its position as a leader in the manufacturing industry and is poised for future success.
Top Co2 Foam Xps Extrusion Board Line
Best Co2 Foam Xps Extrusion Board Line Revolutionizes the Insulation IndustryThe insulation industry has seen a significant advancement with the introduction of the best Co2 foam XPS extrusion board line by [Company Name]. This innovative technology is expected to revolutionize the way insulation boards are manufactured and utilized.[Company Name] is a renowned leader in the field of extrusion technology, with a track record of delivering innovative solutions for the building and construction industry. The company has always been committed to developing sustainable and energy-efficient products, and the best Co2 foam XPS extrusion board line is a testament to that commitment.The new Co2 foam XPS extrusion board line utilizes advanced technology to produce high-quality insulation boards that offer superior thermal performance and energy efficiency. The Co2 foam technology is a game-changer in the industry, as it significantly reduces the environmental impact of the manufacturing process by utilizing carbon dioxide as a blowing agent instead of conventional hydrocarbons.The Co2 foam XPS extrusion board line is designed to meet the growing demand for sustainable building materials that not only provide excellent insulation but also reduce the overall carbon footprint of construction projects. With a focus on energy efficiency and environmental sustainability, the new technology is expected to play a key role in driving the transition towards greener and more sustainable building practices.In addition to its environmental benefits, the best Co2 foam XPS extrusion board line offers superior thermal performance and moisture resistance, making it an ideal choice for a wide range of construction applications. The insulation boards produced by this new technology provide excellent thermal insulation, ensuring energy savings and a comfortable indoor environment for building occupants.Moreover, the Co2 foam XPS extrusion board line is highly versatile and can be used in various construction projects, including residential, commercial, and industrial buildings. Its lightweight and easy-to-install nature make it a preferred choice for architects, contractors, and building owners looking for durable and efficient insulation solutions.[Company Name] has always been at the forefront of innovation in the extrusion technology industry, and the best Co2 foam XPS extrusion board line is a testament to the company's dedication to pushing the boundaries of sustainable building materials. With its focus on sustainability, energy efficiency, and superior performance, the new technology is set to redefine the insulation industry and pave the way for a more sustainable future in construction.The best Co2 foam XPS extrusion board line is a result of [Company Name]'s extensive research and development efforts, as well as its commitment to delivering high-quality products that meet the evolving needs of the construction industry. The company's relentless pursuit of innovation has led to the successful development of this groundbreaking technology, which is poised to make a significant impact on the way insulation boards are manufactured and utilized.In conclusion, the introduction of the best Co2 foam XPS extrusion board line by [Company Name] represents a major milestone in the insulation industry. This innovative technology is set to revolutionize the way insulation boards are produced and used, offering a sustainable and energy-efficient solution for the construction industry. With its superior thermal performance, environmental benefits, and versatility, the Co2 foam XPS extrusion board line is poised to lead the way towards a greener and more sustainable future in construction.
XPS Insulation Foam Making Machine: Get Certified and Competitive Pricing
The demand for energy-efficient and sustainable building materials has been steadily increasing in recent years. As a response to this demand, {Company Name} has developed a state-of-the-art XPS insulation foam making machine that has recently received CE certification.This certification is a significant achievement for the company, as it demonstrates that their XPS insulation foam making machine meets the high safety, health, and environmental protection requirements set out by the European Economic Area. This certification not only validates the quality and reliability of {Company Name}'s machine but also opens up new opportunities for the company to expand its presence in the European market.The XPS insulation foam making machine is designed to produce high-quality XPS insulation foam, which is widely used in the construction industry for its superior thermal and moisture resistance properties. With the CE certification, {Company Name} can now offer its innovative machine to European customers, who can be assured of its compliance with the EU standards for safety and environmental protection.The CEO of {Company Name} expressed his excitement about the CE certification, stating that it is a testament to the company's commitment to delivering top-notch products that meet the highest industry standards. He also emphasized the importance of the European market for {Company Name}'s growth and expansion plans, and how the CE certification will help them to strengthen their position in this key market.In addition to the CE certification, {Company Name} also takes pride in its advanced manufacturing facilities and highly skilled workforce. The company has invested heavily in research and development to ensure that their XPS insulation foam making machine incorporates the latest technological advancements and innovations in the field of insulation materials. This commitment to excellence has enabled {Company Name} to establish itself as a leading provider of cutting-edge solutions for the construction industry.Furthermore, {Company Name} places a strong emphasis on customer satisfaction and support. They offer comprehensive training and technical assistance to their clients, ensuring that they can fully harness the capabilities of the XPS insulation foam making machine and maximize their production efficiency. This dedication to delivering value-added services has earned {Company Name} a stellar reputation in the industry and a loyal customer base.Looking ahead, {Company Name} is optimistic about the prospects for its CE-certified XPS insulation foam making machine. With the European market in its sights, the company is gearing up to seize the opportunities that come with the CE certification and further strengthen its position as a leading provider of innovative insulation solutions.In conclusion, the CE certification of {Company Name}'s XPS insulation foam making machine marks a significant milestone for the company and opens up new possibilities for growth and expansion. With its focus on quality, innovation, and customer satisfaction, {Company Name} is well-positioned to capitalize on the opportunities in the European market and solidify its reputation as a trusted partner for sustainable and energy-efficient construction materials.
PVC Laminated Gypsum Board for Ceiling: Sizes 595*595mm and 603*603mm Available
PVC Laminated Ceiling Gypsum Board Market: Increasing Use in Construction Industry Drives GrowthAs construction projects continue to surge all around the globe, the market for PVC laminated gypsum board is expected to witness a substantial rise in demand. The use of these boards has been gaining momentum over the years, particularly in the construction industry, due to their superior characteristics that make them an ideal solution for ceilings and walls.PVC laminated gypsum board is a type of highly durable and versatile material that has applications in commercial, industrial, and residential settings. They are known for their thermal insulation properties, excellent fire resistance, easy installation, and aesthetic appeal. Furthermore, they provide an additional layer of protection when used on walls and ceilings, offering remarkable sound absorption and moisture resistance.Factors Driving the Growth of PVC Laminated Gypsum Board MarketOver the past few years, the growing demand for these boards in various industrial applications has played a significant role in driving the market's growth. One of the prominent factors driving this demand is the increasing use of these boards in the construction industry, thanks to their high-performance characteristics.Moreover, the availability of these boards in different shapes, sizes, and finishes has made them an ideal solution for commercial and residential applications. With the ongoing development of modern infrastructure, such as airports, commercial buildings, and shopping malls, the demand for PVC-laminated gypsum boards continues to grow.Furthermore, increasing investment in infrastructural development in emerging economies like India and China is one of the critical drivers of the PVC laminated gypsum board market. Rising disposable income and an increasing number of urban centers are also expected to fuel market growth in the coming years.Additionally, as various environmental regulations are implemented across the globe to reduce carbon emissions, the use of PVC laminated gypsum boards helps in reducing these emissions significantly. PVC laminated gypsum boards are an eco-friendly and sustainable solution that reduces energy consumption, making them an ideal choice for achieving green building ratings such as LEED and BREEAM.Competitive LandscapeMajor players operating in the PVC laminated gypsum board market globally include Saint-Gobain S.A., Knauf, USG Corporation, etc. These companies are expanding their production capacities to cater to the growing demand across various end-users such as healthcare, education, hospitality, and residential.Furthermore, they are also adopting strategies like mergers and acquisitions, partnerships, and collaborations to expand their product offering and increase their foothold in the market. For instance, in 2020, Knauf entered into an agreement to acquire USG Corporation in a bid to expand its product offerings in North America.ConclusionPVC-laminated gypsum boards are versatile building materials with a wide range of applications in the construction industry. Their exceptional properties, such as thermal insulation and fire resistance, have made them an ideal solution for walls and ceilings. The market for PVC-laminated gypsum board is set to grow in the coming years due to the increasing use in various end-user industries such as healthcare, education, and hospitality. The entry of new players and the expansion of production capacities of existing players will further propel market growth.
How to Start a Mineral Fiber Ceiling Tiles Manufacturing Plant?
reporting the factory's production line.Mineral Fiber Ceiling Tiles Machine Factory is a renowned name in the manufacturing industry, specializing in producing mineral fiber ceiling tiles. The factory is equipped with state-of-the-art machinery and highly qualified personnel, providing a wide range of products that meet the diverse needs of its customers. The company has established itself as a leader in the industry, focusing on innovation, quality, and customer satisfaction.The manufacturing process at Mineral Fiber Ceiling Tiles Machine Factory is a well-structured and seamless operation. Starting with the raw materials, a mixture of mineral wool, perlite, and other raw materials is blended to create the base material used in making the tiles. The base material is then sent to a forming machine, which molds the material into a flat surface before it is trimmed to the desired size. The excess material is collected and recycled, making the production process environmentally friendly.Once the tiles are formed, they are sent to a drying oven, where they are allowed to dry and firm up. This crucial step ensures that the tiles are strong enough to withstand handling and installation. After drying, the tiles are sanded and inspected to ensure compliance with the strict quality standards set by the factory.The next stage of the production process involves painting the tiles to enhance their aesthetic appeal. Mineral Fiber Ceiling Tiles Machine Factory uses high-quality paint that is resistant to scratches and peels. The painting process is done using automated machinery, which ensures consistency in color and texture across all the tiles. After painting, the tiles are sent to a curing oven, where they are allowed to dry and cure, making the paint permanent.The final stage of the production process involves packaging and shipping the tiles to customers. Mineral Fiber Ceiling Tiles Machine Factory uses state-of-the-art packaging machinery that ensures that the tiles reach the customers in perfect condition. The packaging materials used are eco-friendly, and special care is taken to label the packages accurately, ensuring that the correct number of tiles is delivered to customers.Mineral Fiber Ceiling Tiles Machine Factory is known for its commitment to quality and innovation. The factory invests heavily in research and development, continually seeking to improve the quality of its products and innovate new designs that meet the changing needs of its customers. The factory's team of engineers and designers is always on the lookout for new technologies and techniques that can improve the production process and ensure that customers get the best value for their money.In conclusion, Mineral Fiber Ceiling Tiles Machine Factory is a leading manufacturer of mineral fiber ceiling tiles, providing high-quality products to customers all over the world. The factory's commitment to innovation and quality has made it a preferred choice for customers who demand the best in terms of durability, functionality, and aesthetics. The factory's modern production line, comprising state-of-the-art machinery and highly skilled personnel, is a testament to its dedication to delivering exceptional results that meet the highest standards. Mineral Fiber Ceiling Tiles Machine Factory is setting the pace for the industry and remains a model for other factories to emulate.