Affordable 12mm Calcium Silicate Board Production Line Price List
By:Admin
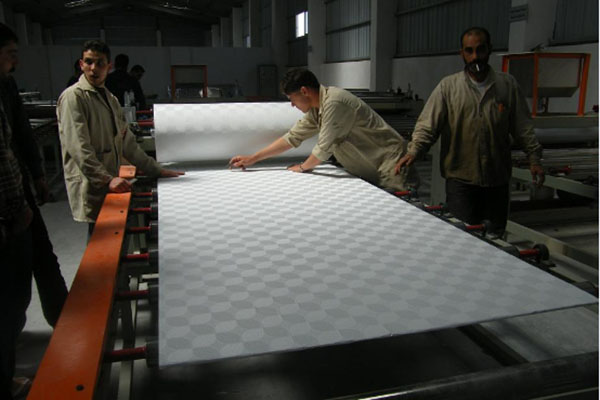
The 12mm Calcium Silicate Board Production Line is designed to meet the increasing demand for high-performance building materials in the market. With its advanced technology and efficient manufacturing process, the production line is capable of producing calcium silicate boards with a thickness of 12mm, which are ideal for various applications in the construction industry. These boards are known for their high strength, durability, and resistance to fire, making them a popular choice for building projects that require reliable and long-lasting materials.
The company's new production line is equipped with state-of-the-art machinery and equipment, allowing for the efficient and cost-effective manufacturing of calcium silicate boards. This ensures that customers can benefit from high-quality products at a competitive price, making it an attractive option for contractors, builders, and developers looking to optimize their construction budgets without compromising on quality.
In addition to offering a competitive price list for its new production line, the company also emphasizes the importance of sustainability and environmental responsibility in its manufacturing process. The 12mm Calcium Silicate Board Production Line is designed to minimize waste and maximize resource efficiency, ensuring that the production of calcium silicate boards is carried out in an environmentally friendly manner. This aligns with the company's commitment to sustainability and its efforts to reduce the environmental impact of its operations.
The company's dedication to quality and customer satisfaction is reflected in its extensive experience in the industry. With a strong track record of delivering reliable and durable building materials, the company has built a solid reputation for excellence, earning the trust and loyalty of its customers. This reputation is further solidified with the introduction of the new 12mm Calcium Silicate Board Production Line, which showcases the company's continued focus on innovation and product development to meet the evolving needs of the construction industry.
By offering a competitive price list for its new production line, the company aims to make high-quality calcium silicate boards more accessible to a wider range of customers. This not only benefits contractors and builders who require cost-effective solutions for their projects but also contributes to the overall advancement of the construction industry by promoting the use of reliable and durable building materials.
In conclusion, the release of the new 12mm Calcium Silicate Board Production Line with a competitive price list reflects the company's ongoing commitment to excellence, innovation, and sustainability. By combining advanced technology with efficient manufacturing processes, the company is able to offer high-quality construction materials at a competitive price point, meeting the needs of a diverse customer base. With its strong reputation in the industry and dedication to customer satisfaction, the company is well-positioned to make a significant impact in the construction sector with its new production line.
Company News & Blog
Customized Abs Board Extrusion Line for XPS Heat Insulation Foamed Plate Production
Qingdao JBD Machinery is a leading manufacturer and supplier of extrusion lines that are used to produce various types of foam boards. With the advanced technology and cutting-edge machinery, the company provides a diverse range of innovative and high-performance extrusion lines to meet the growing demands of the market. The Factory Customized Abs Board Extrusion Line and XPS Heat Insulation Foamed Plate Production Line are some of its popular products with excellent performance and high reliability.The Factory Customized Abs Board Extrusion Line is designed to produce high-quality ABS foam boards, which can be used in a variety of applications such as automotive dashboards, instrument panels, and interior parts. The machine is equipped with a high-quality screw and barrel that ensures the homogeneity and consistency of the mixing process. The production line is also equipped with a precision cut-off system that produces a precise cut and ensures the uniformity of the board thickness.The XPS Heat Insulation Foamed Plate Production Line is one of the best products offered by Qingdao JBD Machinery. The extrusion line is designed to produce lightweight and strong XPS foamed boards, which are widely used as heat insulation and soundproofing materials in construction, refrigeration, and packaging industries. The board offers incomparable heat insulation traits, non-water absorption, high compressive strength, excellent heat preservation performance, and low cost. The foamed plate production line is easy and quick to execute, making it an ideal solution for various industrial applications.The XPS Heat Insulation Foamed Plate Production Line is a fully automatic extrusion line with high productivity and efficiency. The machine is equipped with a high-quality screw and barrel that ensures the uniformity of the foaming process and the homogeneity of the foam structure. The production line also features a precise cutting system that produces high-quality foam boards with uniform thickness and size. The machine can be customized according to customer requirements and can produce boards of different sizes and shapes.Qingdao JBD Machinery is committed to providing customers with high-quality products and services. The company has a team of highly qualified professionals who have extensive experience in manufacturing and designing extrusion lines. The company also provides excellent after-sales service to ensure customer satisfaction. As a leading manufacturer in China, the company has been exporting its products to different parts of the world, including North America, South America, Europe, Asia, Africa, and Oceania. The company has established long-term relationships with its customers by providing them with high-quality products, prompt delivery, and excellent service. In conclusion, Qingdao JBD Machinery is a reputable and reliable manufacturer of extrusion lines that produces high-quality products such as Factory Customized Abs Board Extrusion Line and XPS Heat Insulation Foamed Plate Production Line. The company is committed to providing innovative and cost-effective solutions to its customers, and its products are widely used in various industrial applications. With its cutting-edge technology and excellent service, Qingdao JBD Machinery is poised to become a leading player in the extrusion line manufacturing industry.
Quality Wood Plastic Door Production Line for Board, Profile, and Frame Manufacturing in China
Wood Plastic Door Production Line (Board/Profile/Frame) China ManufacturerAs people become more aware of environmental issues and sustainable resources, there has been a growing demand for innovation in the construction industry. One of the latest trends taking the industry by storm is the wood plastic door production line. This technology combines the benefits of wood and plastic to create a durable and eco-friendly material that's perfect for doors, frames, and profiles. In this article, we'll explore the benefits of this technology and the leading China manufacturer of wood plastic door production line.What is a Wood Plastic Door Production Line?A wood plastic door production line is a modern manufacturing technology that combines natural wood fibers with plastic to create a composite material that's durable, lightweight, and eco-friendly. The wood fibers come from sustainable sources like sawdust, wood chips, or agricultural waste, which are then mixed with thermoplastic materials like PVC, PE, or PP. The resulting composite material has a higher strength-to-weight ratio than traditional wood and is resistant to water, decay, and insects.The wood plastic door production line can produce a range of products, including boards, profiles, and frames. These products can be used for different applications, such as doors, windows, decking, fencing, and more. The wood plastic composite products have a natural wood-like appearance and can be painted or stained to match any design requirement.Benefits of a Wood Plastic Door Production Line1. Eco-Friendly: One of the main benefits of a wood plastic door production line is that it's eco-friendly. The use of sustainable materials like wood fibers and recycled plastics reduces the carbon footprint of the production process and helps preserve natural resources. Moreover, the wood plastic composite products are recyclable, which further enhances their sustainability.2. Durability: Another benefit of a wood plastic door production line is that it produces products that are durable and long-lasting. The composite material is resistant to water, decay, and insects, which makes it ideal for outdoor applications. The products have a longer lifespan than traditional wood and require less maintenance, which saves time and money in the long run.3. Design Versatility: Wood plastic door production line can produce a wide range of designs and color options. The natural wood-like appearance of the products gives them a warm and inviting look, and they can be painted or stained to match any design requirement. The products can be molded into different shapes and sizes, which gives designers more flexibility in their projects.China Manufacturer of Wood Plastic Door Production LineIf you're looking for a reliable manufacturer of wood plastic door production line in China, then look no further than (need remove brand name). As a leading manufacturer and supplier of composite machinery, they have years of experience in the industry and are committed to providing high-quality products and services to customers worldwide.Their wood plastic door production line is designed to produce fireproof, waterproof, and eco-friendly products that meet international standards. The production line can manufacture a wide range of products, including boards, profiles, and frames, that are suitable for indoor and outdoor applications.Their wood plastic door production line is equipped with advanced machinery, such as twin-screw extruders, cooling baths, and cutting machines. The production process is fully automated, which ensures quality control and reduces the risk of errors.ConclusionIn conclusion, the wood plastic door production line is a modern technology that combines the benefits of wood and plastic to create a durable and eco-friendly material that's perfect for doors, frames, and profiles. The products produced by this line are eco-friendly, durable, and versatile, making them an ideal choice for designers and builders. If you're looking for a reliable manufacturer of wood plastic door production line in China, then (need remove brand name) is your go-to source. Their products are designed to meet international standards, and they're committed to providing high-quality products and services to customers worldwide.
Affordable XPS Foam Board Making Machine: Find a Competitive Pricelist
Title: Revolutionary XPS Foam Board Making Machine Redefines Manufacturing EfficiencySubtitle: Pioneering Company Leads the Way in Sustainable and Cost-effective Insulation Production[City], [Date] - The demand for energy-efficient and eco-friendly construction materials has been growing steadily in recent years. In response to this market need, a renowned manufacturing company, with years of industry experience, has introduced an innovative XPS Foam Board Making Machine that revolutionizes the production process. This advanced technology brings forth a range of benefits, including increased efficiency, reduced costs, and enhanced sustainability.The XPS Foam Board Making Machine, developed by [Company Name], is an automated manufacturing solution that simplifies and optimizes the production of extruded polystyrene (XPS) foam boards. XPS foam boards have become popular for their exceptional insulation properties, moisture resistance, and durability. However, traditional manufacturing methods for XPS foam boards were often labor-intensive, time-consuming, and environmentally unfriendly.Recognizing these challenges, [Company Name] has developed an intuitive and fully automated machine that streamlines the entire production process. Equipped with cutting-edge technology and extensive customization options, this XPS Foam Board Making Machine addresses the limitations of conventional manufacturing practices.One of the key features of this machine is its ability to create XPS foam boards of different thicknesses and sizes, catering to various construction requirements. With precise control over dimensions, the machine ensures consistent quality, eliminating wastage and reducing overall production costs. Additionally, the machine's user-friendly interface allows operators to easily monitor and adjust the manufacturing parameters, promoting efficiency and accuracy.The XPS Foam Board Making Machine incorporates state-of-the-art heating and cooling systems, ensuring optimal results with minimal energy consumption. By utilizing smart insulation technology, the machine reduces heat loss during the production process, resulting in significant energy savings. This eco-friendly approach aligns with global efforts to combat climate change and reduces the carbon footprint associated with traditional manufacturing methods.[Company Name], with its commitment to sustainable practices, also emphasizes the usage of environmentally friendly materials. The machine utilizes bio-based blowing agents, thereby eliminating the use of hazardous chemicals in the insulation production. This advancement not only enhances the safety of workers but also contributes to the concept of green construction.Furthermore, the XPS Foam Board Making Machine incorporates advanced quality control mechanisms to uphold stringent industry standards. Real-time monitoring systems and automated sensors detect any deviations in parameters, ensuring consistent product quality throughout the manufacturing process. This attention to quality guarantees exceptional insulation properties and durability, meeting the demands of discerning customers.With a focus on customer satisfaction, [Company Name] also offers comprehensive technical support and expert guidance to their clients. They provide training sessions for operating the machine, troubleshooting assistance, and ongoing maintenance services to ensure a seamless production experience.The introduction of the XPS Foam Board Making Machine by [Company Name] is set to revolutionize the insulation manufacturing industry. This innovative technology promises increased efficiency, reduced costs, improved product quality, and enhanced sustainability. As construction practices shift towards energy-efficient and environmentally friendly materials, this cutting-edge machine presents itself as a game-changer in the market.About [Company Name]:[Include company's introduction here. Mention their expertise in manufacturing and commitment to sustainable practices. Highlight their track record of delivering high-quality products and exceptional customer service.]In conclusion, the XPS Foam Board Making Machine is a revolutionary advancement in manufacturing technology, delivering exceptional efficiency, sustainability, and cost-effectiveness. With its focus on quality control, customizable options, and eco-friendly production, this machine positions [Company Name] as an industry leader in the insulation manufacturing sector.
High Quality PVC Laminated Gypsum Ceiling Board - 595*595 603*603mm
On May 15, 2021, a new product was launched by a renowned construction materials company, a PVC laminated gypsum board that has gained significant attention in the market. This new product promises to revolutionize the construction industry and serve as an answer to the demand for innovative and quality materials.The PVC laminated gypsum board, available in two standard sizes- 595*595mm and 603*603mm, is designed to meet the needs of builders and architects looking to create an exquisite and elegant interior design for their projects. This gypsum ceiling tile is made from high-quality paper-faced gypsum board and then laminated with PVC materials.The PVC laminate on the board provides a smooth and uniform surface while no dust will be generated during the installation process, which makes it a clean and simple installation option. This feature saves time and allows the builders to achieve excellent coverage with low costs, making the PVC laminated gypsum board more reasonable in pricing than other similar products available in the market.The PVC laminated gypsum board offers a durable finish with excellent finish coordination for the entire design scheme. Its waterproof and fire resistance properties make it suitable to install in areas with a high risk of moisture and fire, such as kitchens and bathrooms, medical facilities, and laboratories.Additionally, it is designed to provide insulation, which limits the spread of noise throughout the building, making it ideal for commercial and residential buildings. Its unique surface characteristic reduces the effect of impact sounds and eliminates any problems of sound reverberation providing a comfortable interior space for customers.This new building material solution is also highly customizable, and therefore ideal for creative and artistic designs, which open up new possibilities for building interiors. This means that it is possible to achieve any desired appearance, whether traditional or modern, bright or subtle, matt or glossy, by choosing from a wide range of colors, patterns, and finishes. As a result, it is perfect for use in a range of environments, including luxurious hotel rooms, sport centers, offices, shopping malls, and government buildings. The PVC laminated gypsum board has passed numerous environmental tests, and has been certified as a green material, meaning that it is safe for both builders and customers. It is made from natural resources, which make it a sustainable option for future generations while also meeting the LEED requirements for green building construction standard.The launch of the PVC laminated gypsum board is a significant milestone for the building construction industry. The availability of such a high-quality material that meets all the needs and functions required of today's modern interior design has to come as a welcome development. The advance technology and creativity that went into developing this building material are evident in its outstanding features and design quality, which makes it suitable for a wide range of applications.In conclusion, the PVC laminated gypsum board is a game-changer not only for interior design but also for sustainable building construction. It offers impressive benefits with its durability, waterproofing properties, insulations, and ability to reduce noise and fire hazards making it a perfect choice for builders, architects, and homeowners alike. If you want a building material for your project that combines affordability, superior quality, and sustainability, then the PVC laminated gypsum board is the right choice for you.
Affordable Fully Automatic Gypsum Plaster Cornice Manufacturing Machine Factories
Title: Introduction of Budget-Friendly, Fully Automatic Gypsum Plaster Cornice Manufacturing MachinesIntroduction:In a bid to streamline the manufacturing process and cater to the growing demand for decorative gypsum plaster cornices, a number of factories have introduced cost-effective, fully automatic gypsum plaster cornice manufacturing machines. These high-tech machines have revolutionized the industry, allowing manufacturers to produce high-quality cornices efficiently, while maintaining affordable pricing, thus benefiting both consumers and businesses.Company Overview:One such company, with extensive experience in the manufacturing and supply of gypsum plaster cornice manufacturing machines, has become a pioneer in this industry. With a strong focus on research and development, this company has consistently delivered state-of-the-art machines that automate the previously complex and time-consuming manufacturing processes. Their commitment to affordability and quality has made them a go-to choice for factories looking to enhance their production capabilities.Efficiency and Cost-Effectiveness:The fully automatic gypsum plaster cornice manufacturing machines have significantly increased productivity rates, reducing the overall manufacturing time. These machines are capable of seamlessly producing intricate cornice designs with precision, surpassing previous manual methods. By eliminating human error and minimizing material wastage, manufacturers can save both time and money.Furthermore, these machines have an automated plaster mixing system, which ensures consistent plaster quality throughout the production process. This eliminates the need for manual plaster mixing, greatly enhancing efficiency and productivity. The use of fully automatic machines also allows factories to expand their production capabilities without the need for additional labor, contributing to a well-optimized manufacturing operation.Quality and Customization:Despite the affordability of these machines, there is no compromise on the quality of the final product. The automated process ensures consistent and precise results, guaranteeing the highest standards of craftsmanship. Additionally, manufacturers can customize the machines to create unique designs, enabling them to cater to a wider range of customer preferences.The machines offer a high degree of flexibility, allowing manufacturers to produce cornices of various sizes and styles. This versatility ensures that there is a cornice for every architectural need, be it modern, traditional, or contemporary. By minimizing limitations in design and sizing, these machines enable businesses to meet diverse market demands, ultimately driving growth and profitability.Sustainable Manufacturing:In line with the increasing emphasis on sustainable practices, many manufacturers are now incorporating eco-friendly features into their gypsum plaster cornice manufacturing machines. These machines are designed to minimize energy consumption and reduce waste. By prioritizing sustainable manufacturing, factories can not only contribute to the preservation of the environment but also enhance their brand reputation.Conclusion:The introduction of affordable, fully automatic gypsum plaster cornice manufacturing machines has revolutionized the industry. The combination of efficiency, cost-effectiveness, quality, and customization makes these machines invaluable to manufacturers seeking to meet the demands of an ever-evolving market. As more factories adopt this technology, the production of gypsum plaster cornices is expected to become more accessible and diverse, benefitting both businesses and consumers alike.
High-Quality Decorative Plastic Ceiling Tiles Made from PVC Gypsum Board Building Material
Decorative Plastic Ceiling Tiles: A High Quality Building MaterialWhen it comes to designing the interior of a building, one of the most important elements to consider is the ceiling. The right ceiling can enhance the overall look and feel of a space, and one of the most popular choices for modern buildings are Decorative Plastic Ceiling Tiles. These tiles are made from durable and high-quality PVC material, which not only offers a sleek and modern aesthetic but also offers several benefits over traditional ceiling options.One of the significant advantages of Decorative Plastic Ceiling Tiles is their flexibility and versatility. They come in a wide range of designs and patterns that can match the style and decor of any space. This is in contrast to conventional ceiling materials that tend to be concrete or drywall, which are limited in terms of customization and pattern options.Another advantage of Decorative Plastic Ceiling Tiles is that they are lightweight and easy to install. This makes them ideal for use in both residential and commercial buildings. The installation process is also relatively straightforward and can be done by a professional or a competent DIYer. The tiles can be easily cut to fit the size and shape of the ceiling and can be installed using adhesive or clips.The durability of Decorative Plastic Ceiling Tiles is another factor that makes it a popular choice. They are made from high-quality PVC, which is resistant to moisture, mold, and mildew. This makes them perfect for use in spaces where humidity and dampness are an issue, such as bathrooms, kitchens, and basements.One of the most popular types of Decorative Plastic Ceiling Tiles is the PVC Gypsum Board Building Material. This is a type of ceiling tile that is made from a combination of gypsum and PVC, which provides an even more substantial and durable ceiling option. Gypsum provides excellent fire resistance and sound insulation properties, making it ideal for use in commercial and public buildings.To produce high-quality PVC Gypsum Board Building Material, manufacturers often use Gypsum Ceiling Tile Making Machines. These machines are designed to produce gypsum boards that are strong, durable, and have excellent finished surfaces that offer an attractive finish.In conclusion, Decorative Plastic Ceiling Tiles are a high-quality building material that offers several advantages over traditional ceiling options. With their flexibility, lightweight, and easy installation, they are an excellent choice for both residential and commercial buildings. The PVC Gypsum Board Building Material is particularly durable and reliable, making it an ideal choice for buildings where safety and security are top priorities. With the help of Gypsum Ceiling Tile Making Machines, the manufacturing process can be streamlined, resulting in high-quality and cost-effective ceiling tiles.
Affordable 12mm Calcium Silicate Board Production Line Price List
A leading manufacturer of building materials, has recently released its new 12mm Calcium Silicate Board Production Line, offering a competitive price list for customers looking for high-quality construction materials. The company has established a strong reputation in the industry for producing reliable and durable products, and their new production line reaffirms their commitment to providing top-notch solutions for the construction sector.The 12mm Calcium Silicate Board Production Line is designed to meet the increasing demand for high-performance building materials in the market. With its advanced technology and efficient manufacturing process, the production line is capable of producing calcium silicate boards with a thickness of 12mm, which are ideal for various applications in the construction industry. These boards are known for their high strength, durability, and resistance to fire, making them a popular choice for building projects that require reliable and long-lasting materials.The company's new production line is equipped with state-of-the-art machinery and equipment, allowing for the efficient and cost-effective manufacturing of calcium silicate boards. This ensures that customers can benefit from high-quality products at a competitive price, making it an attractive option for contractors, builders, and developers looking to optimize their construction budgets without compromising on quality.In addition to offering a competitive price list for its new production line, the company also emphasizes the importance of sustainability and environmental responsibility in its manufacturing process. The 12mm Calcium Silicate Board Production Line is designed to minimize waste and maximize resource efficiency, ensuring that the production of calcium silicate boards is carried out in an environmentally friendly manner. This aligns with the company's commitment to sustainability and its efforts to reduce the environmental impact of its operations.The company's dedication to quality and customer satisfaction is reflected in its extensive experience in the industry. With a strong track record of delivering reliable and durable building materials, the company has built a solid reputation for excellence, earning the trust and loyalty of its customers. This reputation is further solidified with the introduction of the new 12mm Calcium Silicate Board Production Line, which showcases the company's continued focus on innovation and product development to meet the evolving needs of the construction industry.By offering a competitive price list for its new production line, the company aims to make high-quality calcium silicate boards more accessible to a wider range of customers. This not only benefits contractors and builders who require cost-effective solutions for their projects but also contributes to the overall advancement of the construction industry by promoting the use of reliable and durable building materials.In conclusion, the release of the new 12mm Calcium Silicate Board Production Line with a competitive price list reflects the company's ongoing commitment to excellence, innovation, and sustainability. By combining advanced technology with efficient manufacturing processes, the company is able to offer high-quality construction materials at a competitive price point, meeting the needs of a diverse customer base. With its strong reputation in the industry and dedication to customer satisfaction, the company is well-positioned to make a significant impact in the construction sector with its new production line.
PVC Foam Board Extrusion Line Machine with CE and ISO Certification: A Comprehensive Introduction
Qingdao Suke Machinery Co., Ltd., a well-known manufacturer of plastic extrusion machinery, has recently introduced a PVC foam board extruder machine with CE and ISO, aimed at catering to the growing demand for quality foam board products across the world. The PVC foam board extrusion line machine is equipped with advanced features that ensure high efficiency and quality output, making it the ideal choice for beginners looking to produce foam board products.The Foam Board Production Line is equipped with SJSZ 45/90 extruder, which has a maximum output of 180kg/h, making it suitable for small to medium scale production. The machine is made using high-quality materials and adheres to international standards, ensuring durability and reliability. The production line is also equipped with a variety of components such as a feeder, calibration table, tractor, and cutting unit, which work in unison to produce high-quality foam board products.The machine is easy to use, making it a popular choice for beginners. It has a user-friendly touch screen interface that allows operators to control all aspects of the production process, from raw material feeding to final product cutting. The machine also has an automatic cutting system, which helps to save time and reduce wastage.The Foam Board Production Line is suitable for producing a wide range of foam board products, including advertising boards, furniture boards, and building materials. The end products have a smooth surface, high density, good strength and rigidity, making them ideal for versatile applications.Talking about the company, Qingdao Suke Machinery Co., Ltd. is a leading manufacturer of plastic extrusion machinery, catering to a wide range of industries such as packaging, construction, automobiles, and more. The company has been in business for over a decade, and its machines are known for their premium quality, innovative designs, and high-level automation. Qingdao Suke Machinery Co., Ltd. has built a global reputation for its commitment to customer satisfaction, providing reliable service and support to each of its clients.With the introduction of the PVC foam board extruder machine, Qingdao Suke Machinery Co., Ltd. is further expanding its range of plastic extrusion machinery, catering to a growing demand for foam board products. The company's commitment to quality, reliability, and innovation makes it the ideal partner for businesses looking to invest in plastic extrusion machinery.In conclusion, the PVC foam board extruder machine with CE and ISO introduced by Qingdao Suke Machinery Co., Ltd. is a high-quality production line that offers a reliable and efficient solution for foam board production. The machine is easy to use, making it a popular choice for beginners, and is suitable for producing a wide range of foam board products. With its commitment to customer satisfaction, Qingdao Suke Machinery Co., Ltd. is the ideal partner for businesses looking to invest in plastic extrusion machinery.
High quality PVC laminated gypsum ceiling tiles machine factories
PVC Laminated Gypsum Ceiling Tiles Machine Factories have been making headlines recently, and for good reason. These factories are at the forefront of producing high-quality, versatile, and durable ceiling tiles that are perfect for a variety of applications. With their state-of-the-art machinery and innovative techniques, these factories are changing the game when it comes to ceiling tile production.One such factory that has been making waves in the industry is the one operated by {}. With years of experience and a commitment to excellence, this factory has become a leader in the production of PVC laminated gypsum ceiling tiles. Their dedication to quality and customer satisfaction has set them apart from the competition and has helped them to establish a strong reputation in the industry.The machinery used in the production process is one of the key factors that sets this factory apart. With advanced technology and precision engineering, they are able to produce ceiling tiles that are not only visually stunning but also incredibly durable and long-lasting. This is essential for a product that is designed to provide both aesthetic appeal and practical functionality in a variety of settings.In addition to their cutting-edge machinery, the factory also prides itself on its commitment to sustainability. They are continually looking for ways to minimize their environmental impact and reduce waste in the production process. This dedication to sustainability has earned them recognition and praise from both customers and industry peers, and has further solidified their position as a forward-thinking and responsible manufacturer.One of the most impressive aspects of this factory is the level of customization and flexibility they offer. Their machinery is capable of producing a wide range of sizes, designs, and finishes, allowing them to meet the unique needs and preferences of their customers. Whether it's a sleek, modern look for a commercial space or a more traditional aesthetic for a residential setting, this factory can deliver the perfect ceiling tiles for any project.It's not just the machinery and production capabilities that make this factory stand out, however. The team behind the operation is equally impressive. Comprised of skilled and knowledgeable professionals, they bring a level of expertise and attention to detail that is second to none. From the initial design phase right through to the final quality checks, every member of the team is dedicated to ensuring that the end product meets the highest standards.With all of these factors combined, it's easy to see why PVC Laminated Gypsum Ceiling Tiles Machine Factories, such as the one operated by {}, are making such a big impact in the industry. Their commitment to quality, sustainability, customization, and customer satisfaction has earned them a strong reputation and a loyal customer base. As they continue to push the boundaries of what is possible in ceiling tile production, there's no doubt that they will remain a force to be reckoned with in the years to come.
Revolutionary Automatic Equipment for Gypsum Board Cornice Production
Title: Revolutionizing Gypsum Board Cornice Production with Innovative Automatic Equipment Introduction:In the rapidly evolving construction industry, technological advancements continue to drive innovation and revolutionize traditional manufacturing processes. Among these innovations, the introduction of automatic equipment for gypsum board cornice production has emerged as a game-changer. This breakthrough solution, developed by an industry-leading company, is set to streamline production, enhance efficiency, and guarantee superior quality in the production of gypsum board cornices.Revolutionizing the Gypsum Board Cornice Manufacturing Process:The new automatic equipment, developed by an industry leader (), simplifies the labor-intensive and time-consuming process of creating gypsum board cornices. This cutting-edge equipment combines advanced technology with precision engineering to bring unprecedented efficiency to the production line. With its innovative features, the device is poised to transform the gypsum board cornice production landscape.Efficiency and Precision through Automation:The automatic equipment boasts an impressive array of features that optimize productivity and ensure consistent quality. Through automation, it eliminates the need for manual labor, significantly reducing production time and costs. By automating key steps such as gypsum mixture preparation, molding, drying, and finishing, the equipment guarantees precise and flawless results.Moreover, this state-of-the-art machinery eliminates human errors, such as inconsistencies in measurements and imprecise cutting. By adhering to pre-programmed instructions, the device ensures standardized dimensions and shapes for each cornice produced. This not only enhances the visual appeal of the final product but also reduces wastage, thus contributing to a greener and more sustainable manufacturing process.Intuitive Control System for Seamless Operation:The automatic equipment incorporates an intuitive control system that enables operators to effortlessly manage and monitor the entire production process. The user-friendly interface provides easy access to crucial parameters such as temperature, humidity, and drying time, allowing operators to make necessary adjustments on the go.Furthermore, the equipment's control system includes built-in safety features to safeguard operators and the overall production line. From emergency stops to error detection, the system effectively mitigates potential risks, ensuring a safe working environment for all involved.Reliable Durability and Low Maintenance:One of the key advantages of this automatic equipment is its exceptional durability. Constructed from high-quality materials and engineered to withstand demanding production environments, this equipment promises longevity and minimal downtime. Additionally, the machinery requires minimal maintenance and is built to withstand daily wear and tear, further reducing operational costs and maximizing productivity.The Company's Commitment to Innovation:The company behind this revolutionary automatic equipment has a strong focus on research and development to meet the ever-evolving needs of the construction industry. With years of experience and a track record of excellence, they have established themselves as pioneers in their field.By continuously investing in cutting-edge technologies, the company strives to push boundaries and exceed customer expectations. Their commitment to innovation is clearly showcased by the introduction of this groundbreaking automatic equipment, which revolutionizes gypsum board cornice production.Conclusion:The introduction of automatic equipment for gypsum board cornice production marks a significant milestone in the construction industry. With its ability to streamline manufacturing processes, enhance efficiency, and guarantee superior quality, this innovation promises to reshape the way gypsum board cornices are produced. As construction companies look for ways to improve their operation's efficiency and output, this automatic equipment provides an ideal solution that not only optimizes productivity but also ensures remarkable precision and consistency.