- Home
- Blog
- Efficient Calcium Silicate Panels Production Line Unveiled - Enhances Manufacturing Process for High-Quality Output
Efficient Calcium Silicate Panels Production Line Unveiled - Enhances Manufacturing Process for High-Quality Output
By:Admin
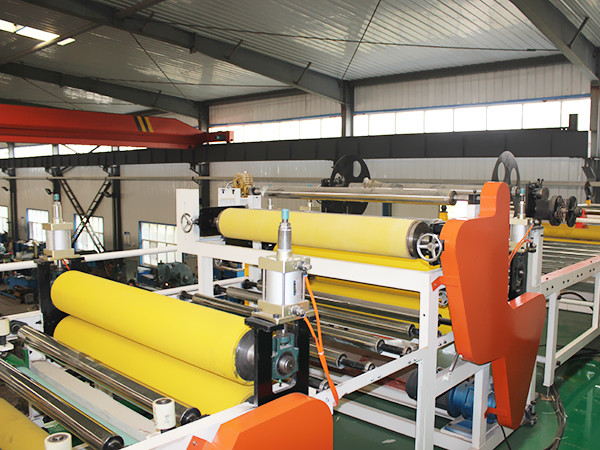
{Company Name}, a renowned manufacturer and supplier of building materials, has recently introduced a state-of-the-art Calcium Silicate Panels Production Line. The company's newest production line is equipped with advanced technology and automated machinery that ensures precision, efficiency, and quality in the manufacturing process.
According to the company spokesperson, Calcium Silicate Panels are widely used in construction due to their exceptional durability, heat resistance, and sound insulation properties. They are also easy to install and require minimal maintenance, making them an ideal choice for various commercial and residential applications.
"In response to the growing demand for high-quality Calcium Silicate Panels, we have invested in a technologically advanced production line that enables us to manufacture panels that meet the highest industry standards. Our new production line is capable of producing panels of various sizes and thicknesses, catering to the diverse needs of our clients," said the spokesperson.
The Calcium Silicate Panels Production Line comprises a range of automated machinery, including a hydraulic press, a mixer, a slurry tank, a slicing machine, and a drying chamber. The machinery is connected through a computerized control system that regulates the entire production process, from raw material mixing to packaging.
With an annual production capacity of 2 million square meters, the production line is expected to significantly boost the company's production output and fulfil the increasing demand for Calcium Silicate Panels in the market.
{Company Name} is known for its commitment to delivering high-quality building materials at affordable prices. The company uses state-of-the-art technology and the latest production techniques to ensure that its products are consistent in quality and performance.
The company's Calcium Silicate Panels are made from a combination of Portland cement, finely ground silica, cellulose fibers, and other mineral additives. The panels undergo a rigorous quality control process to ensure that they meet the required industry standards.
According to the spokesperson, Calcium Silicate Panels are gaining popularity in the construction industry due to their many benefits over traditional building materials. They are non-combustible, resistant to fire and moisture, and provide excellent sound insulation and thermal insulation. They are also eco-friendly, as they are made from natural materials and can be recycled.
"Calcium Silicate Panels are an innovative solution for modern construction needs. They offer exceptional durability, safety, and thermal performance, making them ideal for use in various applications, such as partition walls, ceilings, cladding, and flooring," said the spokesperson.
In conclusion, {Company Name}'s introduction of a Calcium Silicate Panels Production Line is a significant step towards meeting the increasing demand for high-quality, eco-friendly building materials. The company's commitment to innovation, quality, and affordability is evident in its investment in advanced technology and machinery. With the new production line, the company is poised to become a leading supplier of Calcium Silicate Panels in the market, offering its clients a wide range of options that cater to their distinct needs and preferences.
Company News & Blog
Calcium Silicate Board Production Line - Hard Board Making Machine - Building Material Manufacturing Machinery - Product Details on Kskuntai.com
Hebei, China - Kskuntai.com, a leading manufacturer of building materials, has announced the release of its state-of-the-art Calcium Silicate Board Production Line. This cutting-edge technology is designed to facilitate the production of high-quality Calcium Silicate Boards that meet international standards.The Calcium Silicate Board Production Line is a vital part of the overall manufacturing process. This innovative machinery is designed to produce a variety of building materials, including Hard Board, Calcium Silicate Board, and several others. The production line is a fully automated system that ensures that the final product is of the highest quality, with a smooth surface, uniform thickness, and precise edges.One of the unique features of this production line is that it can handle different board thicknesses and sizes with ease. The company uses advanced technology in board making, which ensures that each board is of consistent quality with excellent mechanical performance and insulation properties. The production line also has a high yield, with low energy consumption, making it an efficient and cost-effective solution for manufacturing Calcium Silicate Boards.In addition, this production line is equipped with a variety of safety features to create a safe working environment. The line has advanced monitoring systems to ensure that the machine is running smoothly at all times. There are also emergency shutdown systems in place that can immediately bring the machine to a halt in case of any malfunction.According to an official from Kskuntai.com, “Our Calcium Silicate Board Production Line is the result of our commitment to excellence. We believe that it is our responsibility to provide our customers with the best possible quality products. Our production line is not only efficient but also eco-friendly. We have taken several steps to ensure that it is energy-efficient and minimizes waste.”The Calcium Silicate Board Production Line is a significant addition to Kskuntai.com’s range of manufacturing solutions. With this latest technology, the company can produce high-quality Calcium Silicate Boards to meet the growing demand for eco-friendly and sustainable building materials. These Calcium Silicate Boards are ideal for use in walls, ceilings, floors, and various other applications in the construction industry.Kskuntai.com is a leading manufacturer and supplier of building materials, operating in over 30 countries worldwide. The company prides itself on providing innovative and reliable solutions to its customers. With a focus on quality, efficiency, and sustainability, the company continues to demonstrate its commitment to excellence.In conclusion, the Calcium Silicate Board Production Line is a cutting-edge technology that has a significant impact on the construction industry. Kskuntai.com’s latest machinery ensures the production of high-quality Calcium Silicate Boards that meet international standards. With its energy-efficient and eco-friendly features, the production line is an efficient and sustainable solution for the manufacture of building materials.
Effective Slurry Distribution for Multiple Screens: PU Dewatering Screen with Vibrating Motor
As the demand for high-quality mineral fiber ceiling board increases, so does the need for efficient and reliable production equipment. Fortunately, there are now several top-grade Mineral Fiber Ceiling Board Machine factories that offer state-of-the-art production machinery and systems designed to meet the demands of modern manufacturing.One of the best ways to achieve high-quality ceiling boards is by using mineral fiber materials, which are known for their sound absorption, fire resistance, and thermal insulation properties. These materials are derived from naturally occurring minerals, such as basalt, perlite, and volcanic rock, which are then processed and combined with various binders, such as starch or resin.To produce mineral fiber ceiling boards, a Mineral Fiber Ceiling Board Machine is used to mix and form the materials into panels or tiles of varying sizes and densities. These machines utilize advanced technologies, such as heating and pressing, to create a strong and durable product that meets the required specifications.When selecting a Mineral Fiber Ceiling Board Machine factory, it is essential to consider some critical factors that will ensure optimal performance, reliability, and cost-effectiveness. Some of these factors include:Quality of the MachinesA high-quality Mineral Fiber Ceiling Board Machine should be durable, reliable, and easy to operate. The quality of the materials used in the manufacturing process is also critical, as low-quality materials can lead to frequent breakdowns and maintenance issues.Production CapacityThe production capacity of the Mineral Fiber Ceiling Board Machine should meet the needs of your manufacturing facility. It is essential to choose a machine that can handle your desired output without compromising on quality or efficiency.Maintenance and SupportChoosing a reputable Mineral Fiber Ceiling Board Machine factory that offers reliable maintenance and technical support ensures minimal downtime and maximum productivity. It is essential to choose a factory that provides regular maintenance and repair services and offers quick response times in case of any technical issues.Cost-effectivenessThe cost of the equipment and its maintenance should be within your budget. Choosing a Mineral Fiber Ceiling Board Machine factory that offers affordable solutions without compromising on quality or efficiency is critical to the success of your manufacturing plant.ConclusionMineral fiber ceiling board production has come a long way in recent years, thanks to advanced Mineral Fiber Ceiling Board Machine technology. By selecting a quality Mineral Fiber Ceiling Board Machine factory, you can ensure that your manufacturing plant produces high-quality, cost-effective, and efficient mineral fiber ceiling boards. Contact a reputable factory today to get the best mineral fiber ceiling board production machinery for your facility.
New Equipment for Manufacturing MGO Board Announced
Innovative Mgo Board Equipment to Revolutionize Construction IndustryA new Mgo board equipment is poised to revolutionize the construction industry. The advanced manufacturing technology offered by this equipment is designed to deliver top-quality Mgo board products for various building applications.The equipment, whose name cannot be disclosed for competitive and legal reasons, has been developed by a leading manufacturer of Mgo board and related products. The company has been producing high-quality Mgo board for more than a decade, and has gained a solid reputation for delivering top-rated products.With a focus on innovative design and advanced technology, the company's new Mgo board equipment combines precision engineering, high-quality components, and user-friendly features that are intended to make the manufacturing process more efficient and cost-effective.The equipment features a robust workstation that is easy to operate, with a user-friendly interface that provides seamless control and precise measurement. The workstation is designed to process Mgo boards of various sizes and thickness, ensuring that the output meets the required specifications.The Mgo board equipment also features advanced mixing technology, which is essential for producing high-quality Mgo boards. The mixing process is automated and controlled, resulting in a consistent and uniform mixture that meets the required standards.In addition, the equipment is equipped with advanced cutting technology, which ensures that the Mgo boards are accurately cut to the required size and shape. The cutting process is automated and precise, providing clean and smooth edges for the finished product.One of the standout features of the new Mgo board equipment is its innovative automation capabilities. The equipment is designed to automate most of the manufacturing process, reducing the need for manual labor and minimizing the risk of human error. This results in a more efficient and cost-effective production process, while also ensuring consistently high-quality Mgo board products.Moreover, the equipment is designed to be environmentally friendly, with reduced energy consumption and minimal waste. This is achieved through advanced energy-saving technology and improved production processes that optimize material usage, while minimizing waste.The company prides itself on being committed to sustainability and environment-friendly manufacturing practices. All of its products are ISO certified, ensuring that they meet the highest standards of quality and safety.With the introduction of the new Mgo board equipment, the company aims to provide its customers with an even better experience and more high-quality products. The equipment is already in high demand, with several orders already placed by both local and international customers.The company believes that the new Mgo board equipment is poised to transform the construction industry by delivering high-quality and sustainable building materials. The company's dedication to innovation, quality, and sustainability has been one of the driving factors behind its success and continued growth in the industry.In conclusion, the new Mgo board equipment is a game-changer for the construction industry. With its advanced technology and innovative features, it promises to deliver high-quality and sustainable building materials that meet the needs of today's modern construction projects. As the demand for environmentally friendly and cost-effective building materials continues to grow, the company's new Mgo board equipment is perfectly positioned to lead the way.
Efficient Calcium Silicate Panels Production Line Unveiled - Enhances Manufacturing Process for High-Quality Output
Calcium Silicate Panels Production Line Introduced by {Company Name}{Company Name}, a renowned manufacturer and supplier of building materials, has recently introduced a state-of-the-art Calcium Silicate Panels Production Line. The company's newest production line is equipped with advanced technology and automated machinery that ensures precision, efficiency, and quality in the manufacturing process.According to the company spokesperson, Calcium Silicate Panels are widely used in construction due to their exceptional durability, heat resistance, and sound insulation properties. They are also easy to install and require minimal maintenance, making them an ideal choice for various commercial and residential applications."In response to the growing demand for high-quality Calcium Silicate Panels, we have invested in a technologically advanced production line that enables us to manufacture panels that meet the highest industry standards. Our new production line is capable of producing panels of various sizes and thicknesses, catering to the diverse needs of our clients," said the spokesperson.The Calcium Silicate Panels Production Line comprises a range of automated machinery, including a hydraulic press, a mixer, a slurry tank, a slicing machine, and a drying chamber. The machinery is connected through a computerized control system that regulates the entire production process, from raw material mixing to packaging.With an annual production capacity of 2 million square meters, the production line is expected to significantly boost the company's production output and fulfil the increasing demand for Calcium Silicate Panels in the market.{Company Name} is known for its commitment to delivering high-quality building materials at affordable prices. The company uses state-of-the-art technology and the latest production techniques to ensure that its products are consistent in quality and performance.The company's Calcium Silicate Panels are made from a combination of Portland cement, finely ground silica, cellulose fibers, and other mineral additives. The panels undergo a rigorous quality control process to ensure that they meet the required industry standards.According to the spokesperson, Calcium Silicate Panels are gaining popularity in the construction industry due to their many benefits over traditional building materials. They are non-combustible, resistant to fire and moisture, and provide excellent sound insulation and thermal insulation. They are also eco-friendly, as they are made from natural materials and can be recycled."Calcium Silicate Panels are an innovative solution for modern construction needs. They offer exceptional durability, safety, and thermal performance, making them ideal for use in various applications, such as partition walls, ceilings, cladding, and flooring," said the spokesperson.In conclusion, {Company Name}'s introduction of a Calcium Silicate Panels Production Line is a significant step towards meeting the increasing demand for high-quality, eco-friendly building materials. The company's commitment to innovation, quality, and affordability is evident in its investment in advanced technology and machinery. With the new production line, the company is poised to become a leading supplier of Calcium Silicate Panels in the market, offering its clients a wide range of options that cater to their distinct needs and preferences.
Affordable WPC Door Board Production Machine - PE Profile Extrusion Line Introduction PE profiles are commonly used in windows, wall panels, and decorative applications. This extrusion line offers an ideal solution for producing these profiles. The line comprises a conical twin-screw extruder, mould, calibration table, hauler, cutter, and stacker. Moreover, for PE window profiles, the line includes a co-extruder.
In the world of extrusion machines, JEEBO Machinery is a name that stands out for their precision and quality. If you're looking for a reliable and efficient PVC PE profile extrusion line, then JEEBO Machinery's Factory Cheap Hot Wpc Door Board Making Machine is the perfect choice.PVC profiles are in high demand for creating windows, wall panels, and small decorative profiles. With the Factory Cheap Hot Wpc Door Board Making Machine, you can produce all these profiles with ease. This machine is manufactured with top-of-the-line conical twin screw extruders, moulds, calibration tables, haulers, cutters, and stackers to ensure the best quality output.The extruder is the core component that handles the PVC material and transforms it into the desired shape and size. With JEEBO Machinery's conical twin screw extruder, you'll get superior results and efficient processing speeds. The machine's precision mould ensures that every product comes out uniformly and meets the required specifications.Once the profile is formed, it needs to be cooled and calibrated before being cut into the required size. JEEBO Machinery's calibration table gives you full control over the cooling process, resulting in a proper shape and size. The hauler moves the profile through the machine with precision and accuracy, while the cutter ensures that the final product is accurately sized. The stacker collects the finished product in an organized manner, making the packaging and transportation process smooth and seamless.JEEBO Machinery's Factory Cheap Hot Wpc Door Board Making Machine is not only efficient, but it also offers high-quality output at an affordable price. The machine is also versatile enough to handle PVC material with or without brand names. In addition, JEEBO Machinery's Cheap Xps Foam Board Extrusion Line is an excellent choice for producing foam boards. This machine is easy to operate, efficient, and produces high-quality foam board extrusions that meet the required standards. The machine is easy to maintain and is built with durable and long-lasting materials, making it an excellent investment for your business.In conclusion, JEEBO Machinery is a reputable and trustworthy company that produces reliable and efficient extrusion machines. If you're looking for a premium PVC PE profile extrusion line or a cheap XPS foam board extrusion line, JEEBO Machinery has got you covered. With their quality and affordable products, you can rest assured that your business is in good hands.
XPS Foam Board Production Line for Plastic Product Making Machinery Industry with Advanced Features
Xps Foam Board Making Equipment: The Future of Sustainable ConstructionIn the world of construction, insulation plays a vital role in achieving energy efficiency, cost savings, and environmental sustainability. And when it comes to insulation materials, XPS foam boards are quickly gaining popularity over traditional insulation materials thanks to their superior compressive strength, moisture resistance, and insulation performance. But what makes XPS foam board production possible? The answer is simple: XPS foam board making equipment.XPS foam board making equipment is an innovative machinery that allows manufacturers to produce high-quality XPS foam boards in a faster, more efficient, and cost-effective manner. It is a machine that melts polystyrene resin and injects it with a blowing agent to create foam beads. These beads are then molded into XPS foam boards of various sizes and thicknesses using a series of machines and processes.One of the main features of XPS foam board making equipment is its use of programmable logic controllers (PLC) and computer controls. These advanced systems not only make the operation of the machines more convenient and simple, but they also ensure that the production process is highly precise and accurate. The use of touchscreens and visual flow charts also makes it easy for operators to monitor and adjust the entire production process for quality control and optimization.Another notable feature of XPS foam board making equipment is its screw injection system. This system allows for precise control over the amount of vesicant or blowing agent that is injected into the mix. This results in foam boards that have uniform and consistent cell structures, which translates to better insulation performance and durability.One of the major advantages of XPS foam board making equipment is the versatility it offers in terms of the types of foam boards that it can produce. The equipment can make XPS foam boards of different thicknesses and densities, making it ideal for a wide range of applications, from roof insulation to underfloor heating and beyond. It can also be used to produce different types of foam boards such as flat, tapered, or cut to the required shape.When it comes to sustainability, XPS foam board making equipment is quickly becoming a game-changer. XPS foam boards are largely made of polystyrene resin, which is a non-biodegradable material that can have significant environmental impacts if not properly handled. However, by producing XPS foam boards with advanced machinery, manufacturers can significantly reduce the amount of waste and emissions associated with conventional foam board production processes.In conclusion, XPS foam board making equipment is a crucial component in the production of sustainable and high-performing insulation materials. With its advanced controls, screw injection system, and versatility, it offers manufacturers an efficient and effective way of producing XPS foam boards of different types, sizes, and densities. As the world continues to prioritize energy efficiency and environmental sustainability, XPS foam board making equipment will undoubtedly play a significant role in achieving these goals.
China-based Manufacturer Offers PVC Imitation Marble Decorative Sheet Making Machine
Kingshine Plastic Machinery: A Leading Manufacturer in ChinaKingshine Plastic Machinery is a leading manufacturer and supplier of high-quality plastic machinery and equipment. The company is based in China and has over 10 years of experience in the field of plastic machinery. Kingshine Plastic Machinery is committed to providing innovative and cost-effective solutions to customers across the world. In this article, we will focus on one of the company's flagship products, the PVC Imitation Marble Decorative sheet Making Machine.PVC Imitation Marble Decorative sheet Making MachineKingshine Plastic Machinery has introduced its latest product, the PVC Imitation Marble Decorative sheet Making Machine. As per their website, “PVC Imitation Marble Decorative sheet Making Machine is a highly automated manufacturing solution for MS and PC sheets used in various industries.” It is designed to produce sheets with a marble-like finish, which can be used to create decorative panels for a wide range of applications such as flooring, walls, furniture, and more.Features of PVC Imitation Marble Decorative sheet Making MachineThe PVC Imitation Marble Decorative sheet Making Machine is built with the latest technology and state-of-the-art equipment. Some of the features of this machine include:1. High Production Efficiency: The PVC Imitation Marble Decorative sheet Making Machine is capable of producing up to 800 Kg of sheets per hour, making it ideal for large-scale production.2. Versatility: With this machine, users can produce sheets of different sizes and thicknesses depending on their specific needs.3. Easy Operation: The machine is designed for ease of use and requires minimal technical knowledge to operate. It also comes with a user-friendly interface that makes it easier for operators to monitor the production process.4. Energy Efficient: The PVC Imitation Marble Decorative sheet Making Machine is engineered to optimize energy consumption, resulting in significant savings in electricity costs.5. High-Quality Output: The sheets produced by this machine have a marble-like finish, high gloss, and excellent physical properties.Why Choose Kingshine Plastic Machinery?Kingshine Plastic Machinery is a respected name in the plastic machinery industry. The company has been in business for over a decade and has built a reputation for providing high-quality machinery and excellent customer service. Some of the reasons to choose Kingshine Plastic Machinery include:1. Exceptional Quality: All Kingshine Plastic Machinery products are made with high-quality materials and are designed to meet or exceed industry standards.2. Custom Solutions: Kingshine Plastic Machinery understands that every customer has unique needs. As such, the company offers customized machinery solutions tailored to individual customer requirements.3. Competitive Prices: Kingshine Plastic Machinery offers high-quality products at competitive prices, making them an affordable option for businesses of all sizes.4. Excellent Customer Support: The company has a team of knowledgeable and experienced professionals who provide excellent customer support to clients, from initial inquiries to after-sales support.ConclusionThe PVC Imitation Marble Decorative sheet Making Machine is one of the latest offerings from Kingshine Plastic Machinery. With its high production efficiency, versatility, and ease of use, this machine is an excellent investment for businesses seeking to manufacture high-quality sheets for various decorative applications. As a leading manufacturer of plastic machinery, Kingshine Plastic Machinery provides innovative and cost-effective solutions to clients across the world. To learn more about the PVC Imitation Marble Decorative sheet Making Machine and Kingshine Plastic Machinery, visit their website.
Advanced Production Line for High Capacity Mineral Fiber Ceiling Tiles from China
High Capacity Mineral Fiber Ceiling Tiles Production Line Unveiled by Chinese ManufacturerA leading Chinese manufacturer has unveiled its latest product – the High Capacity Mineral Fiber Ceiling Tiles Production Line. The new system is designed to boost the manufacturing process of mineral fiber ceiling tiles, increasing efficiency, speed and output.The production line, produced by China-based machinery and equipment manufacturer, will be available for both commercial and industrial use, with a variety of customizable options to meet a diverse range of production requirements. The product launch represents a new innovation in the construction industry and has met with a lot of interest from manufacturers both within China and internationally.The High Capacity Mineral Fiber Ceiling Tiles Production Line boasts some impressive features, including a high level of automation, precision control, high output capacity, and energy efficiency. These features allow manufacturers to streamline their production processes, save time and energy, reduce production costs while ensuring that quality is not compromised.The production line comprises various core components, including a frame forming machine that forms the tiles' core structure, a dryer unit providing heat treatment to the tiles, and a surface treatment unit that adds a finishing touch to the tiles. The production line also includes a cutting unit, which can cut the tiles to different sizes and shapes.The high-capacity production line's frame forming machine uses a high-precision servo motor, which reduces manufacturing errors and improves efficiency. The dryer unit is equipped with advanced heating technology that can reach temperatures of up to 300 degrees Celsius, ensuring that the tiles are dried quickly and thoroughly. The surface treatment unit is responsible for the tiles' final finish, which can be customized to suit the customer’s requirements.The company behind the production line has a long-standing reputation for producing high-quality machinery and equipment. The firm has been in the industry for many years and has built a strong reputation for quality and reliability. The launch of the new product builds on this reputation and reflects the company’s commitment to innovation and staying up-to-date with the latest technologies and manufacturing processes.The spokesperson for the company highlighted the importance of its latest product launch, stating:"The High Capacity Mineral Fiber Ceiling Tiles Production Line represents a game-changing innovation in the production process of mineral fiber ceiling tiles. The product boasts high efficiency, quality, consistency, and customizability, enabling manufacturers to meet the demands of their customers quickly. We are thrilled to bring this revolutionary product to the market, and we believe it will significantly benefit the construction industry both locally and internationally."The launch of the High Capacity Mineral Fiber Ceiling Tiles Production Line is set to have a positive impact on the construction industry globally, particularly in regions that require a high number of ceiling tiles for use in the construction of buildings. The production line's ability to produce customized tiles in large volumes quickly and efficiently is a significant breakthrough for the manufacture of ceiling tiles, and it is hoped that it will lead to greater efficiency and cost-effectiveness in the construction industry.Overall, the unveiling of the High Capacity Mineral Fiber Ceiling Tiles Production Line is a significant milestone for the manufacturing industry, and it represents a bright future for the construction industry. With its impressive features and innovative technology, the production line is sure to generate interest and lead to greater efficiency and cost-effectiveness in the production of mineral fiber ceiling tiles.
Europe Style for XPS Foam Board Production Line - XPS Foam Sheet Extrusion Line
article about Europe style Xps Foam Board Production Line.In recent years, the demand for Xps Foam Board has rapidly increased due to its excellent thermal insulation properties. Xps Foam Board is a type of insulation material that is widely used in construction industry to reduce energy consumption and keep the buildings warm. To meet the growing demand for Xps Foam Board, JEEBO Machinery has developed a state-of-the-art Xps Foam Board Production Line that is specifically designed to produce high quality and durable Xps Foam Boards.JEEBO Machinery, based in Qingdao, China, is a renowned manufacturer of plastic extrusion machines. With years of experience in the industry, JEEBO Machinery has built a reputation for producing cost-effective and reliable plastic extrusion machines that meet the needs of a wide range of industries. The company's Xps Foam Sheet Extrusion Line is a result of extensive research and development, and is designed to meet the specific production requirements of Xps Foam Board.The Xps Foam Board Production Line by JEEBO Machinery is fully automatic and computerized, ensuring high precision and consistency in the production process. The machine is equipped with advanced technology that allows for the production of multilayer Xps Foam Boards in a variety of thicknesses and densities. The machine is also equipped with a high-performance cooling system that ensures the Xps Foam Boards are cooled quickly and evenly, resulting in a smooth and uniform surface.One of the notable features of JEEBO Machinery's Xps Foam Board Production Line is its ability to produce Xps Foam Boards in the Europe style. The Europe style Xps Foam Board is characterized by its narrow ribs that run parallel to the long edge of the board. This design enables the Xps Foam Board to interlock with each other, creating a tight and secure seal that prevents heat loss. The Europe style Xps Foam Board is also known for its high compression strength, making it suitable for use in high-load applications.The Xps Foam Board Production Line by JEEBO Machinery is fully certified by CE and SGS, ensuring that the equipment meets the highest quality standards. The company's commitment to quality is reflected in its use of high-quality raw materials and components, as well as its rigorous testing and quality control processes.JEEBO Machinery's Xps Foam Board Production Line has received high praise from customers around the world. The machine is known for its efficiency, reliability, and ease of operation, making it a popular choice among manufacturers of Xps Foam Board. The company's after-sales service is also highly regarded, with a team of experienced technicians available to provide technical support and maintenance services.In conclusion, JEEBO Machinery's Xps Foam Board Production Line is a highly advanced and efficient machine that is designed to produce high-quality Xps Foam Boards in the Europe style. The machine's advanced technology, high precision, and consistency in the production process ensure that customers receive Xps Foam Boards that meet the highest quality standards. With its commitment to quality and customer satisfaction, JEEBO Machinery is a leading manufacturer of Xps Foam Board Production Line, and is set to play a key role in the construction industry's transition towards energy-efficient buildings.